Premium Only Content
This video is only available to Rumble Premium subscribers. Subscribe to
enjoy exclusive content and ad-free viewing.
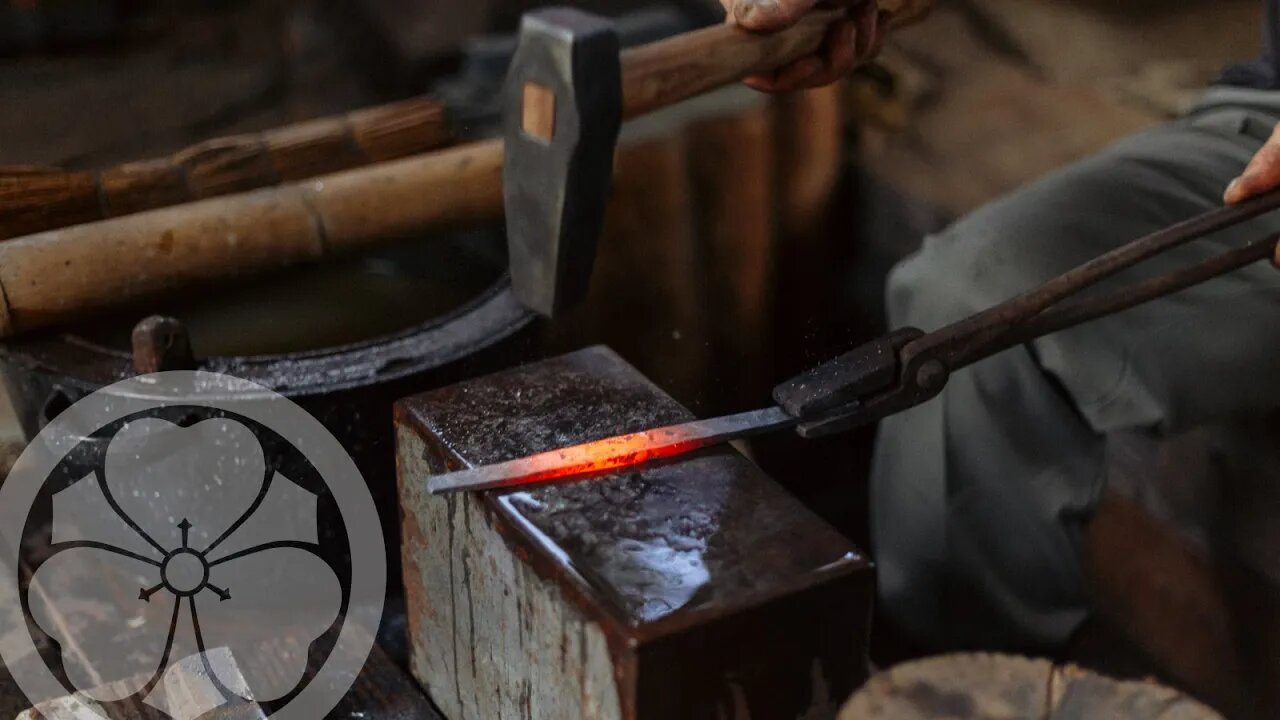
Tools for Satoyama
islandblacksmith
- 2 / 11
1
Short Film – 温故知新 | Study the Old to Know the New | by Trevor Komori
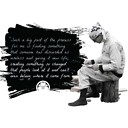
islandblacksmith
In a forge on Vancouver Island, reclaimed steel is turned into handcrafted tanto.
Directed, Photographed, and Edited by Trevor Komori
Location Sound: Sean Brouwer
B Camera Operator: Liam Leyland
Music Composed by Kurtis So
Production Assistants: Vivian Hu & Judy Zheng
still images: https://islandblacksmith.ca/2018/08/short-film-release-%E6%B8%A9%E6%95%85%E7%9F%A5%E6%96%B0/
behind the scenes: https://islandblacksmith.ca/2017/08/komorisan-back-in-the-forge/
forging the sunnobi tanto: https://islandblacksmith.ca/2018/03/utsushi-study-of-a-sunnobi-tanto/
making the tanto mounting: https://islandblacksmith.ca/2017/08/on-ko-chi-shin-tanto/
14.6K
views
The Blacksmith | Tools for Satoyama | by Jordan Wende
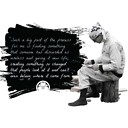
islandblacksmith
Reclaimed antique steel is forged into a kotanto as part of the Satoyama Project. http://islandblacksmith.ca
Directed, Photographed, and Edited by Jordan Wende: https://www.instagram.com/jordanwende/
Photo essay: http://islandblacksmith.ca/2020/07/photo-essay-forging-a-knife/
Finished kotanto: http://islandblacksmith.ca/2021/02/forest-kotanto-with-antique-fittings/
Knife in the intro: http://islandblacksmith.ca/2020/07/kominka-forest-kotanto/
3
SOTW #20 - Assembling the Furusato Tanto (aikuchi w/ireko saya)
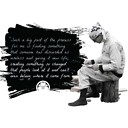
islandblacksmith
Serious students of the forge can watch the full process version here: https://youtu.be/oH5B7n7NtbE
One of the most technical challenges of this project was creating the ireko saya (入れ子鞘, nesting scabbard) lining within the tight constraints offered by the original block of wood. A refined detail that is normally hidden from view, the ireko saya protects the blade from the hardwood. A focal point for the koshirae is the unique antler crown kurikata which is reminiscent of a mushroom contrasting against the dark wood of a tree.
Furusato (故郷, pronounced “foo-roo-sah-toe”) means home place or hometown and contains the ideas of being rooted or grounded wherever one may sojourn, and a confidence and longing for return. This tanto has a simple and elegant form with a natural and humble mounting that reflects the rustic satoyama lifestyle and suits the aesthetics of the way of tea.
The wood was a discarded scrap that was just barely large enough for this project and comes from the Congo/Zaire. The block of wood sat for several years waiting for the right blade to make the best and most use of it. This precious dark chocolate coloured hardwood is locally called Tshikalakala or Dikela, meaning turn around or circle back.
Materials for the wabisabi aikuchi style koshirae mounting include Tshikalakala (Wenge) wood for the kataki tsuka and saya, Hounoki (Japanese Magnolia) wood and cow horn for the ireko saya, copper bus bar for the habaki, buffalo horn for the mekugi, and pieces of shed antler for the kurikata and tsunakuchi. The tsuka and saya are finished in a thin layer of kijiro fukiurushi (wiped lacquer) made from natural source urushi lacquer.
"When difficulties come, I remember my home place…Someday I shall fulfill my task. And, then, return to my home place. To the green mountains and clear rivers of my home."
-- Furusato, Takano Tatsuyuki
More about this project: http://islandblacksmith.ca/2019/08/furusato-tanto/
3.27K
views
4
SOTW #17 - Glass Top Fuigo - What's going on in there?
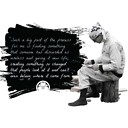
islandblacksmith
A look at the inside operation of a prototype fuigo (鞴) box bellows...two intake valves, two manifold valves, one piston, one output, double action...more about fuigo here: http://islandblacksmith.ca/2015/06/why-you-need-a-swordsmiths-fuigo-box-bellows/
valves: http://islandblacksmith.ca/2015/11/making-valves-for-fuigo-box-bellows/
fuigo archive: http://islandblacksmith.ca/tag/fuigo/
3.72K
views
5
Making a Bamboo Scoop for Water Forging (竹の水差し)
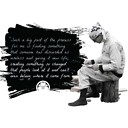
islandblacksmith
Simple technology for pouring water on the anvil, made from a piece of bamboo.
Forging with a thin film of water on the anvil and hammer prevents forge scale or oxide from being hammered into the surface of the steel. The hot steel instantly vaporizes the water and the resulting steam explosion blows the scale off of the work, keeping it clean as it is worked. This type of bamboo scoop (take no mizusashi) is a traditional style tool for evenly applying water to the surface of the anvil or the hot steel.
Unlike steel, forge scale does not move or compress at forging temperatures. If a piece of scale is hammered into the surface of a blade it creates a depression and the entire surface of the blade will have to be filed down to remove the scale and pitting later. Water forging is one way to keep the blade clean and smooth and reduce work and waste during finishing and polishing. Swordsmiths usually keep a bucket of water right next to the anvil to supply water to the surface and to periodically dip the hammer into while working.
This is about the quickest and most useful traditional tool for controlled application of water, taking only minutes to create from natural materials. The best starting point is structural/timber bamboo that is about two inches inside diameter, is not cracked, and has at least one or two nodes or joints in it.
read more about the process: http://islandblacksmith.ca/2015/07/making-a-bamboo-water-scoop-for-water-forging/
4.36K
views
6
TLDW #19 - Bladesmithing at the Museum Swordsmith Forge
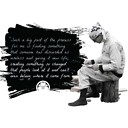
islandblacksmith
**WARNING: This is the longer process version intended for serious students of knifemaking.
The sunobe stage is at 4x speed as the hammering was fairly inaccurate due to a blister on my palm from the seam of the yellow gloves...starting material was a harrow tooth, finished blade is hirazukuri, iori mune, 140mm / 5.5" nagasa, 6.5mm motokasane...more info below...
0:20
1. the harrow tooth is first forged into a sunobe, a blade preform, that has a rectangular cross section with the proper thickness and distal tapers for the spine and tang as well as a small notch where the mune machi will be...(dead battery zone)
2. then the iori mune, the peaked spine, is forged...
3:00
3. then the bevels are forged in, working from the machi towards the tip and then back down again, followed by the forging of the tang in this case...during the beveling stage the spine tends to curve upwards so a stump between the anvil and forge is used to make downwards adjustments in advance from time to time, the wood will not mar the peak of the spine...also during this stage water on the anvil keeps the scale from building up and being forged into the surface of the steel...
7:19
4. the nakago (tang) is also shaped and beveled using the same techniques as the blade...
9:11
5. some final planishing, adjustments, and straightening along with a hot stamp "signature" on the tang bring the hizukuri stage to a close...the finish will be tsuchime (hammer texture) so there was no filing/polishing before yaki-ire...
10:16
6. yaki-ire (quenching/hardening) was done at my own forge for the dim and consistent light conditions, allowing the colour to be seen more accurately...
11:10
7. yaki-modoshi (tempering) is a slight reheating to remove some of the stress and increase toughness after hardening...
http://islandblacksmith.ca/process/
2.83K
views
7
SOTW #15 - Museum Forge Project
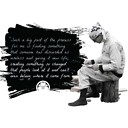
islandblacksmith
Read more about this project here: http://islandblacksmith.ca/2017/01/building-traditional-swordsmith-forge/
Serious students of the forge can watch the full process and see more traditional Japanese swordsmith style forge construction here: https://www.youtube.com/watch?v=Hi9Sh2Dt65U&list=PLBJ5AOs7cMwCSinW7foaiHFZKbZDkasQL&index=1
Most of history was forged with very simple equipment made from found and natural materials. A basic charcoal forge can be made with clay, brick, or even mud and stone.
Traditional Japanese swordsmithing forges are purpose-built with certain design elements specific to the tasks involved in tanren and hizukuri. This is a short overview of a 7 part series to illustrate several of the features that are common to this type of construction and follow the process of crafting a functioning swordsmith’s forge at a museum on Vancouver Island.
3.54K
views
8
A Japanese Media Visit to the Forge
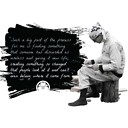
islandblacksmith
(has subtitles in english) Thanks very much to the guys who came all the way to the workshop to film for TV Tokyo. Here is most of my segment which includes footage from the visit as well as some of our own footage shot of charcoal making. Editing 5 hours of footage down to a few minutes is no easy task but they did a great job of telling the story of the workshop and the basic forging process.
Though it was an entertaining point that I had gleaned some of my specialized information by watching Japanese swordsmiths at work on Youtube, I would like to include some additional credits from the interview that did not make the final cut...Emmanuel Schrock for my blacksmithing foundation at age 14, Pierre Nadeau for clarifying and explaining techniques I had seen in practice, Yoshihara~san for his excellent books printed in english, and Louie Mills for inspiration and advice.
Read more about the visit here: http://islandblacksmith.ca/2015/07/japanese-media-visit-the-forge/
9
SOTW #3 - Sounds of the Workshop: Chopping Charcoal (sumi-kiri)
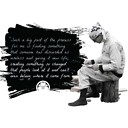
islandblacksmith
breaking in the new camera: this is a brief demo of the process of preparing the finished charcoal for the forge...the larger chunks are split or chopped up and screened to remove the dust...for swordsmithing there are more specific divisions into four sizes from dust to larger pieces for different phases of forging and preparation...most of my work is with 1-2 inch pieces and we generally process the amount of charcoal in that bucket or more in a single batch...the charcoal is softwood, pine is the standard but for general forge work cedar and fir are also acceptable...shot in japan where you can buy pine charcoal, in canada we have to make our own.
1.16K
views
10
SOTW #1 - Sharpening a Nata (variation of a Japanese brush knife)
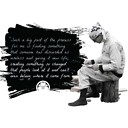
islandblacksmith
grandpa has a half dozen variations of these ancient tools and keeps going back to them despite having newer ones on the shelf...the old ones are hand forged and very thick and sturdy, with an integral rope-wrapped handle and lots of heft...the style can vary from a slightly curved bamboo hatchet shape to a sickle style with deep brush tip...i started with a fairly coarse synthetic stone and then went to a fine natural Japanese finishing stone...shot near Sasayama.
this tool makes a great charcoal chopper if you are using properly cooked softwood that still has lots of strength left in it!
11
ふるさと - furusato, "home place"
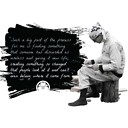
islandblacksmith
A glimpse of daily life at 100 years of age in a small rural village in Japan. Growing chestnut trees, daikon radish, and sweet potatoes as winter turns to spring in the shadow of a mountain forest.
2024, 1080p
The Blacksmith | Tools for Satoyama | by Jordan Wende
3 years ago
739
Reclaimed antique steel is forged into a kotanto as part of the Satoyama Project. http://islandblacksmith.ca
Directed, Photographed, and Edited by Jordan Wende: https://www.instagram.com/jordanwende/
Photo essay: http://islandblacksmith.ca/2020/07/photo-essay-forging-a-knife/
Finished kotanto: http://islandblacksmith.ca/2021/02/forest-kotanto-with-antique-fittings/
Knife in the intro: http://islandblacksmith.ca/2020/07/kominka-forest-kotanto/
Loading comments...
-
LIVE
Jeff Ahern
1 hour agoFriday Freak out with Jeff Ahern (Chainsawing DEI)
386 watching -
46:31
PMG
12 hours agoHannah Faulkner and Mary Flynn | REVIVING THE AMERICAN DREAM - GROWING UP A FLYNN
2.35K -
3:01
Kirill MultitoolOfficial
23 hours ago $3.35 earnedSurvival skills and Bushcraft HACKS in the forest!
30.6K5 -
11:52
Dr. Nick Zyrowski
12 hours agoWhat Can I Eat On The Carnivore Diet? | Detailed Guide
30K4 -
16:23
TSPLY
20 hours agoNew CNN / MSNBC Meltdown Moments Of Getting Mad At Donald Trump And Elon Musk
21K14 -
30:54
Cooking with Gruel
19 hours agoCooking with Matt and Ginger Gaetz
12.3K5 -
1:22:55
MTNTOUGH Fitness Lab
21 hours agoHomeland Security Pulls Us Off The Plane! Jaw-Dropping Moments from MTNTOUGH's 2024 Ibex Hunt
47.3K1 -
1:05:30
Kyle Rittenhouse Presents: Tactically Inappropriate
16 hours ago $0.67 earnedHey Doge, Where's My Coin?
22.8K3 -
4:44
America First Policy Institute
23 hours agoAmerica First Unfiltered: Trump’s Historic First Month – Real Wins for Real Americans! 🇺🇸 #news
26.2K2 -
8:22
DropItLikeItsScott
1 day ago $0.72 earnedThis IS one of the Greatest AR's EVER! The Nemesis by Special Ops Tactical
10.8K2