Premium Only Content
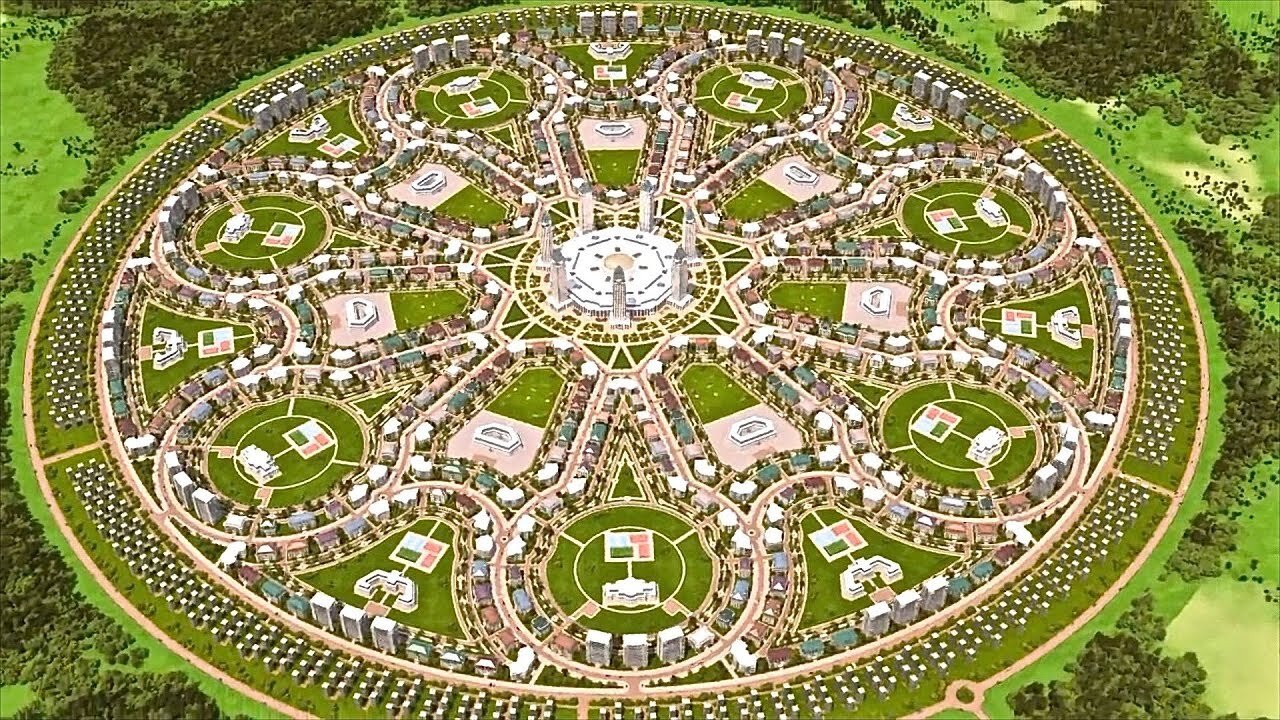
Futuristic Quick Prefab City Construction Technology
Concept by DAHIR INSAAT original links https://www.youtube.com/user/dahirsem/videos ...New Technique: 'Cast-in-Place Panel Construction'. The Dahir Insaat corporation has developed a new construction technique that makes it possible to construct high-quality housing in various architectural styles quickly, and with industrial efficiency. It can also be used to develop a whole district, or even to build a new town.
Our technique combines the plus points of cast-in-place construction with the high quality ensured by factory production of the building's architectural details. The basis of the whole system is a new universal wall panel.
What makes this solution so original is the fact that this panel serves both as an element of the wall and also as part of the supporting column. The column is cast in place within this wall panel.
When the panels are formed, a special gap is left for the column. At the construction site, it is literally 'put onto' the reinforcing steel of what will become the column. Then the gap with the 'rebar column' is filled with concrete. The result is genuine cast-in-place construction: the steel and concrete become a column, and the column is cast to the panel. And the panels themselves are so precise, smooth, and even that they can be joined together safely and easily using adhesive.
The panels are 1,700mm wide. Their height can vary (for instance, 3,100mm, 2,700mm, or 2,500mm) depending on how high the storey is to be.
This kind of 'cast-in-place panel construction' makes it possible to put up reliable, earthquake-resistant buildings of up to 50 storeys. This is achieved by using normal cast-in-place construction, light outer walls, and a large number of columns around the building's perimeter: there can be not just one, but two or three reinforced columns inside each wall panel.
With the help of this new technique, a high speed of construction can be achieved. For example, a one-storey building measuring 25x60 meters (1,200 square meters of usable space) was assembled in five hours. And a team of ten construction workers will need only two months to put up a ten-storey residential building.
Undemanding, and with excellent insulating properties...
The wall panels can be manufactured using a very wide variety of raw materials, which allows them to be produced in any part of the country. For instance, they can be made from light concretes: expanded clay concrete, gas concrete, pumice concrete, vermiculite concrete, or expanded polystyrene concrete. It is also possible to use concrete made with sawdust, wood chip, felt, textile fibres, etc. This gives the panels excellent insulating properties. If desired, all types of insulation in use today can be employed: poured, filled, or laid. The panels are formed and steamed in a horizontal position, which prevents the insulating material from felting during the concrete hardening process.
When the panels have been put onto the steel frame and the concrete poured in, at the construction site, they become a cast-in-place wall along with the overall skeleton of the building.
There can be several columns to one panel, and their shapes can also vary: round, or straight-sided. For instance, a single column of 300mm diameter will suffice for a building of up to three storeys. The assembly can also be done in a different way: first prepare and cast the columns, and only add the panel when you are confident there are no gaps and the column meets the specifications.
Three thousand panels a day!
Our technique is based on industrial manufacturing, at a factory that is almost completely automated.
The steel molds are combined with plastic inserts. These thin reusable inserts form the outer surface of the wall panel. The inserts can be used hundreds of times, and once they start to deteriorate they can be crushed into plastic chips and used to make new molds. These repeated reuse of the plastic lowers the cost of panel production.
White cement is used for the finishing layer of the faсade, giving a high-quality surface.
The molds are cast in a special facility. Each mold is first sprayed with a thin layer of fibre, the composite framework is inserted, and a ceramsite blend is poured on from above. Then vibration is applied, as well as vacuum processing, if required. All the installation details within the mold are already in place, including the ones that leave gaps for the columns.
The panels are placed overnight in containers which also serve as steam chambers, where they acquire 40% resilience. The steam chamber takes account of the temperature required for white cement to set.
-
49:16
Knowledge Land
13 days agoThe Prehistoric Volcano That Nearly Wiped Out All Humanity - Full Documentary
442 -
2:41
ErmiasMeseret
3 years agoAustralian Building construction technology
25 -
6:19
BlackDiamondGunsandGear
22 hours agoHow Fat Guys can Appendix Carry
23.8K2 -
6:58
Gun Owners Of America
1 day ago2024 Was Huge For Gun Rights, Here's Our Top 10 Wins!
25.7K1 -
15:50
Degenerate Jay
1 day ago $1.28 earnedJames Bond Is Being Ruined By Amazon? Make Him A Black Gay Woman?
19.7K9 -
15:18
DeVory Darkins
1 day ago $12.04 earnedTrump Drops NIGHTMARE Warning on Joe Biden
36K44 -
36:13
The Why Files
1 month agoAlien Implants Vol. 1: Devil’s Den UFO Encounter: What Was Found Inside Terry Lovelace?
67.6K39 -
9:03
Alabama Arsenal
1 day ago $0.36 earnedAAC HUB 2K | Modern Features, Iconic Classic Looks
9.7K1 -
13:49
Dermatologist Dr. Dustin Portela
2 days ago $0.67 earnedDermatologist Reveals the Worst Things To Do To Your Skin
7.96K1 -
1:02:24
PMG
23 hours ago $0.22 earned"Hannah Faulkner and Jamie Villamor | DEFEND, INSPIRE, INFLUENCE"
6.56K