Premium Only Content
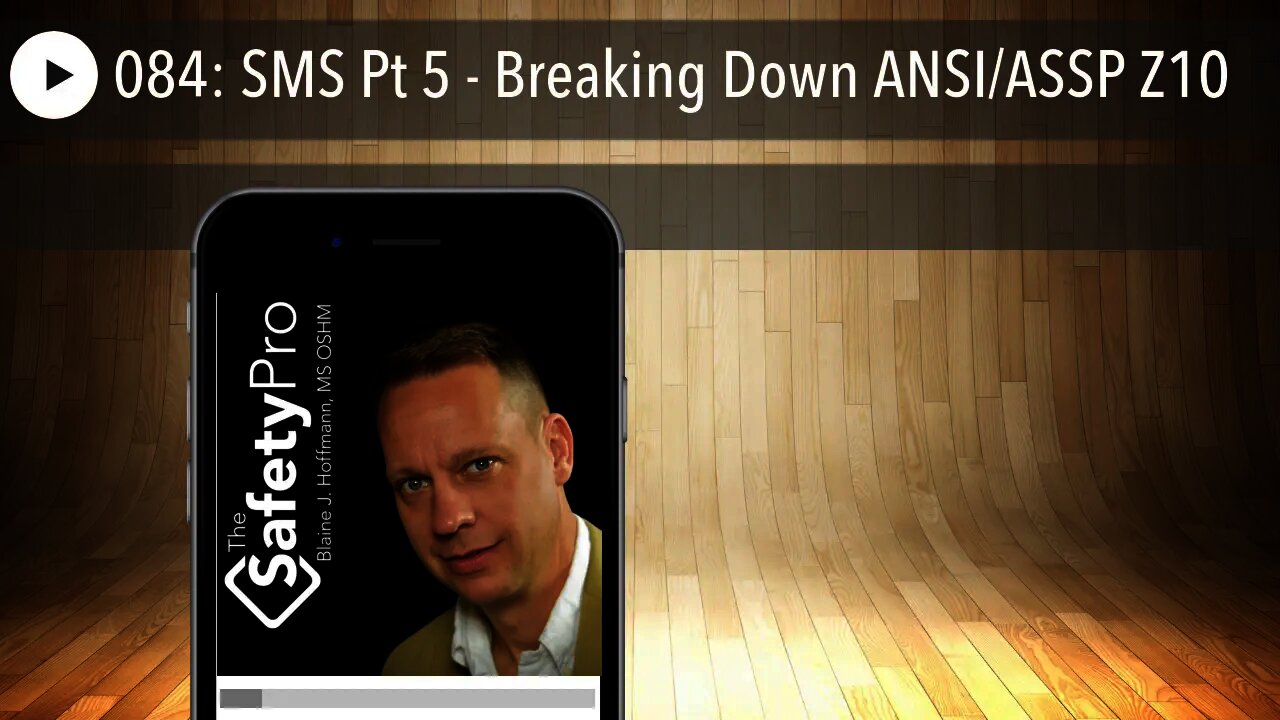
084: SMS Pt 5 - Breaking Down ANSI/ASSP Z10
Subscribe here:
http://www.thesafetypropodcast.com
Powered by iReportSource
We know by now that the application of a safety management system (SMS) can drastically improve organizational safety performance. Even OSHA's Partnership program, VPP, relies on management system principles, and you can see the results that participants encounter on their website.
So, back in 1999, ANSI started a committee to begin work on what would become known as the Z10 standard. The committee looked at existing national and international standards in occupational safety and health. Initially approved in 2005, it was revised once and reaffirmed in 2017. More recently, the collaboration between ANSI and the American Industrial Hygiene Association was replaced on the Z10 committee by the American Society of Safety Professionals (ASSP), which is why you will now see the standard now titled ANSI/ASSP Z10.
ANSI Z10 encourages participants to integrate other management systems with the safety management system. Mainly because most other systems follow the Plan, Do, Check, Act (PDCA) model as the basis for continuous improvement, so it should be familiar to most organizations. Not only that, it is incredibly useful! The stated purpose of the standard is to provide organizations a valuable tool for continuous improvement of their safety and health performance.
The standard focuses mainly on the strategic aspects of policies and the things that go into making sure they are carried out. What ANSI Z10 does NOT do is provide companies with things like detailed procedures and job instructions. So let's get into what is required by this voluntary standard.
Like other voluntary standards, the ANSI/ASSP Z10 is broken down into sections. According to the Table of Contents, the seven sections are as follows:
• Scope, Purpose, & Application
• Definitions
• Management Leadership & Employee Participation
• Planning
• Implementation & Operation
• Evaluation & Corrective Action
• Management Review
Scope, Purpose, & Application
Just as in the case with ISO 45001, ANSI/ASSP Z10 starts with the Scope, Purpose & Application. It defines the minimum requirements for the safety management system, and its primary purpose is, again, to provide a tool that organizations can use to reduce injuries, illnesses, and fatalities. Of course, the standard can be applied to any organization regardless of size and type.
Management Leadership & Employee Participation
The top management has to mandate all parts of the organization to establish, maintain, implement, and maintain the SMS per the standard.
This mandate starts with top management establishing a documented EHS policy. Companies have to make sure that, at a minimum, the safety policy includes the following:
• Protection and continual improvement of employee safety and health.
• Meaningful employee involvement.
• Require conformance with the organization's safety and health program requirements.
• Require compliance with established safety and health laws and regulations.
The top leadership must also accept ultimate responsibility for safety and health by doing the things we come to expect in these safety management systems:
• Provide financial and professional resources to carry out the management system requirements.
• Define roles and responsibilities, accountability, and authority to carry out the management system requirements.
•  Integrate the SMS into other business systems and processes, which includes performance reviews, compensation, rewards, and recognition programs are in line with the SMS.
Employees also have to assume responsibility for parts of the SMS over which they have control, like following safety rules and procedures. All of this must be communicated to all employees as well as be made available to relevant external interested parties.
According to ANSI, top leadership should not only hire a safety professional and delegate all of this to them. They must be visible in their leadership by participating in carrying out aspects of the SMS as well.
Employee Participation
The organization has to establish a process that ensures meaningful employee participation throughout all levels. At a minimum:
• Provide employees the means, time, and resources needed to participate in the planning, implementation, evaluation, corrective action, and preventative actions required by the SMS.
• Provide employees access to information related to the SMS.
• Effectively remove all barriers to meaningful involvement.
ANSI states that the planning process goal is to identify and prioritize SMS issues such as hazards, risks, SMS deficiencies, and opportunities for improvement. The organization must also establish goals and objectives to improve upon the SMS as well.
There are four parts of this section:
• Review Process
• Assessment and Prioritization
• Objectives
• Implementation Plans and Allocation of Resources
Let's talk
-
1:00:02
Dad Dojo Podcast
12 hours ago $1.61 earnedEP28: Teen Stabbed At Track Meet
5.88K2 -
13:49
Mrgunsngear
11 hours ago $3.55 earnedHow many PUBG Cast Iron Skillets Does It Take To Stop A Bullet?
12K11 -
12:01
Clownfish TV
18 hours agoHollywood HELLSCAPE: L.A. is the New DETROIT?!
13.5K15 -
16:05
Nick Freitas
12 hours agoSaving a Billion a Day
11.8K3 -
16:49
CarlCrusher
1 day agoBizarre Secret Mysteries of the Grand Canyon and Colorado River Badlands
13.2K5 -
28:57
Esports Awards
17 hours agoVeracity From Unsung Hero to International Esports Host | Origins Podcast #3
10.8K1 -
6:38
The Official Steve Harvey
18 hours ago $1.06 earnedMy accountant died... I owed 22 million dollars 😱
15.2K7 -
18:05
Degenerate Jay
21 hours ago $1.87 earnedThis Is Ruining Video Game Development
30.6K5 -
26:14
Neil McCoy-Ward
18 hours ago"We've Lost Control!" - (Says FRENCH 🇫🇷 Police Chief..
37.7K26 -
8:19
Rethinking the Dollar
19 hours agoU.S. Debt Warning: The Hidden Risk Forcing a Gold Surge
51.6K2