Premium Only Content
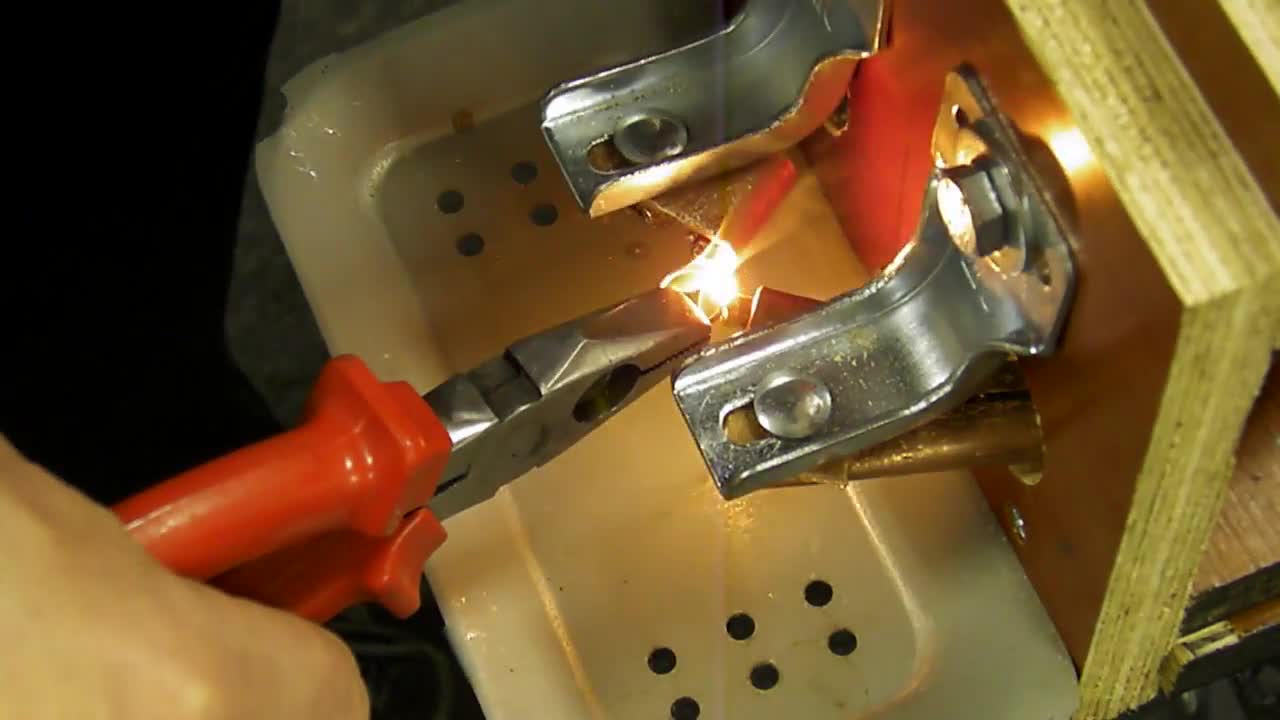
DIY Butt-Flash Welder for Chain Mail Rings Made From Microwave Oven Parts (mainly the MOT)
This is me butt welding a test ring with a DIY Butt/Flash welder made from microwave oven parts.
The wire used in this video is a 1,2 mm diameter SG-2 MIG Welding wire) This gauge of wire is just for the welding device's proof of concept in conjunction with the use of welding wire as the main material for chain mail (jump)rings.
The welding machine is made largely from microwave oven parts.
It uses a rewired Microwave Oven Transformer (MOT) as a low voltage high current power source of about 1150 W.
The primairy coil is unchanged and is (as in the microwave oven) powered by 220V 50/60 Hz AC straight from the wall outlet. The original high voltage secondary coil of the MOT was removed (cut, shissled and bashed out) and replaced by a 1,5 turn 50 mm2 copper coil (insulated wire used is of an automotive origin) which delivers a 1,7 V 50/60 Hz AC open terminal voltage at about 680 A short circuit current. This current can not be measured by me but the value is a theoretical amount and should be about right. The current which will flow if a steel ring is applied is much less (in the 450/500 A range) because steel has a much higher electrical resistance about 20 times as much as copper wire of the same thickness.
The device is essentially an AC resistance welder in which principle the welding heat is generated by means of running an extremely high current across a resistance area, in this case the steel wire pushed against the terminals. A welding principle similar to spot welding.
The body of the machine is made with water resistant 3/4 inch plywood. The terminal mounts are heavy duty central heating radiator supports. The terminals are MIG contact tips with a v-groove filled into the tip. The cable lugs and the terminal mounts are made of copper water pipe (5/8 and 1/2 inch diameter)
The device is actuated with a foot pedal and uses electronics (specifically a relay and a micro switch) salvaged from the same microwave oven. Same goes for the fan, the fuse and filter PCB and the wiring.
How to use this welding machine in regards to welding rings for chain mail:
First of all it is important to have open rings which are manipulated with pliers so that they are flat, the butted join/seam is closed and straight (the best you can) and the cut's surfaces are as flat as possible. This can be done by cutting the rings of the coil (with a saw or a rotating cutting disk) or by "breaking" away the rings from the coil by means of the "score, twist and break" method. I made a short video on how to do this, look for it in my Rumble accountpage.
This latter method of liberating rings from a wound coil, leaves the ring with a surprisingly smooth and flat edge. The resulting seam is smoother and can be butt welded more easily and without any rings self destructing while applying the welding current. Open, uneven or pinch cut (when using a mini bolt cutter or the like) joins tend to arc (and spark) and as a consequence suffer from meld-throughs and possibly pose a fire hazard.
The resulting weld:
The ring welded in this video has a very smooth and even weld area, hardly any burrs or spots. Thought the ring has lost it's protective copper coating (which coating is standard for SG-2 MIG welding wire) the ring is welded very strong. Tests will be performed to determine the strength of both the butted (unwelded) rings and there welded counterparts. These tests will be carried out with the 1,6 mm diameter SG-2 MIG welding wire which is on order.
Eventually I intend to use the larger diameter 1,6 mm SG-2 MIG welding wire for my chain mail garments. 1,6 mm is the largest diameter MIG welding wire which comes on spools. Any larger and the wire is only available as 3-4 feet long rods.
The chain mail pieces I like to be making in the near future are: first of all a coif (a headpiece which extents over the shoulders), followed by a hauberk (long sleeved chain mail shirt which reaches to around or slightly above the knees) and lastly a pair of leg pieces. I expect to be needing two spools of 15 kg Sg2 MIG welding wire, maybe a bit more. The rings I intend to make for my chain mail should end up having a internal diameter (ID) of about 8,5-9,0 mm (I am guessing here because I have a digital calliper on request at Santa's Hardware Store)
Hope you enjoy the video.
Any questions? Please do not hesitate and ask them in the comments...
-
15:41
Your Vaping Dollar
4 years agoClapton wire jig made from parts out of junk draw.
261 -
10:53
metal working and casting
4 years ago $0.02 earnedFoundry Pattern Making from Parts
153 -
1:51
HowStuffWorks_Science
4 years agoStuff of Genius: Percy Spencer: Microwave Oven
148 -
6:29
engineershubspot
4 years ago $0.03 earnedCreate Multiple Parts from One DXF
718 -
7:06
World Tree Tech
4 years agoMystery box from subscriber. More computer parts?
23 -
3:30
WCPO
4 years agoMail carrier delivers message from Santa
13 -
5:47
Dustydavecreations
4 years agoHickory hammer made from offcuts
341 -
1:25
easycooking
4 years agoRibs made in the oven
46 -
LIVE
Dr Disrespect
6 hours ago🔴LIVE - DR DISRESPECT - WARZONE - IMPOSSIBLE TRIPLE THREAT CHALLENGE
3,370 watching -
1:04:05
In The Litter Box w/ Jewels & Catturd
22 hours agoYOU'RE FIRED! | In the Litter Box w/ Jewels & Catturd – Ep. 747 – 2/21/2025
53.6K25