Premium Only Content
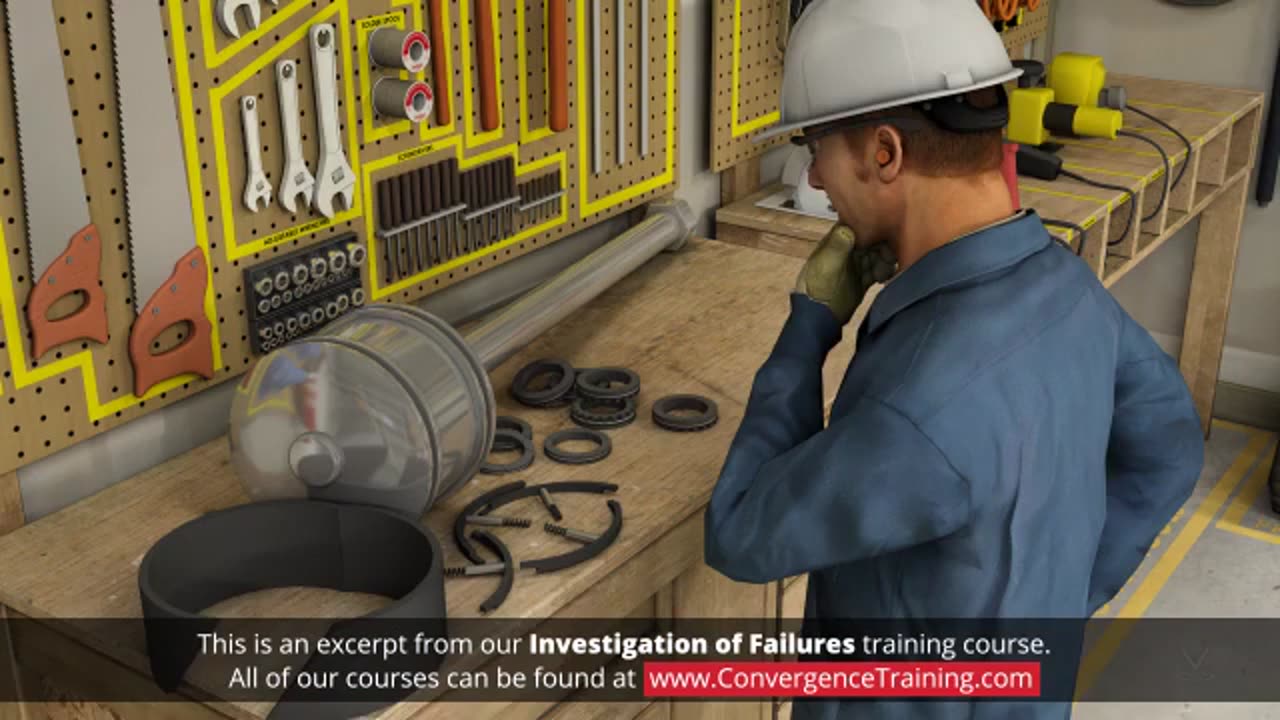
Investigation of Equipment Failures
Investigating equipment failures is a critical process to identify the root cause of malfunctions, prevent recurrence, and improve reliability. A systematic approach ensures that failures are thoroughly analyzed, lessons are learned, and appropriate corrective actions are implemented.
---
### **1. Purpose of Investigating Equipment Failures**
- **Safety**: Prevent injuries or accidents caused by equipment malfunctions.
- **Reliability**: Improve the operational efficiency and lifespan of equipment.
- **Cost Savings**: Avoid downtime, repair costs, and production losses.
- **Compliance**: Meet regulatory and industry standards.
---
### **2. Steps in Equipment Failure Investigation**
#### **a. Immediate Actions**
- **Secure the Scene**: Ensure safety by shutting down and isolating the failed equipment.
- **Document the Failure**: Take photos, videos, and notes of the failure site.
- **Preserve Evidence**: Avoid tampering or altering the failed equipment.
#### **b. Data Collection**
- **Operational Records**: Gather logs, maintenance records, and equipment history.
- **Witness Statements**: Interview operators, maintenance personnel, and other witnesses.
- **Failure History**: Check if similar failures occurred in the past.
#### **c. Initial Assessment**
- Identify the visible damage or symptoms.
- Note any abnormal operating conditions (e.g., vibrations, noise, temperature).
#### **d. Root Cause Analysis**
- **Visual Inspection**: Examine physical damage, wear, and tear.
- **Testing and Diagnostics**: Conduct tests such as non-destructive testing (NDT), vibration analysis, or thermal imaging.
- **Cause Mapping**: Use tools like fishbone diagrams or the 5 Whys technique to trace the root cause.
#### **e. Categorize Causes**
- **Human Error**: Misoperation, lack of training, or poor maintenance.
- **Material Issues**: Defective components or materials.
- **Design Flaws**: Inadequate design or engineering.
- **Environmental Factors**: Corrosion, extreme temperatures, or external impact.
- **Operational Factors**: Overloading, improper use, or lack of lubrication.
---
### **3. Reporting Findings**
- **Failure Summary**: Describe the nature, location, and timing of the failure.
- **Root Cause**: Detail the primary and contributing factors.
- **Impact Assessment**: Analyze the failure’s effect on operations, safety, and costs.
- **Evidence**: Include photos, diagrams, test results, and witness statements.
---
### **4. Corrective and Preventive Actions**
#### **a. Immediate Corrective Actions**
- Repair or replace the failed component.
- Implement temporary fixes to restore functionality.
#### **b. Long-Term Preventive Measures**
- Improve maintenance schedules (e.g., predictive or preventive maintenance).
- Enhance operator training and documentation.
- Address design flaws through engineering changes.
- Use higher-quality materials or components if necessary.
---
### **5. Monitoring and Follow-Up**
- Evaluate the effectiveness of corrective actions.
- Monitor similar equipment for signs of potential failure.
- Update maintenance protocols and training materials as needed.
---
### **6. Investigation Tools and Techniques**
- **Failure Mode and Effects Analysis (FMEA)**: Evaluate potential failure modes and their impacts.
- **Fault Tree Analysis (FTA)**: Trace pathways leading to equipment failure.
- **Root Cause Failure Analysis (RCFA)**: Systematically identify underlying issues.
- **Statistical Tools**: Use reliability data and trends to predict failures.
---
Would you like help creating a detailed investigation report template, checklist, or guide specific to a type of equipment failure?
-
23:39
The Finance Hub
20 hours ago $8.99 earnedI CAN'T BELIEVE WHAT JUST HAPPENED TO ADAM SCHIFF!
29K95 -
9:01
Dr. Nick Zyrowski
13 hours agoThe BIG NAC ( N-Acetyl Cysteine) Mistake
17K1 -
1:02:40
Kyle Rittenhouse Presents: Tactically Inappropriate
14 hours ago $1.63 earnedThe Lectern Bandit
8.98K4 -
8:18
DropItLikeItsScott
15 hours ago $0.34 earnedThe SAR9 SOCOM Optics Ready Pistol is a GAME CHANGER!
6.41K3 -
35:31
The Lou Holtz Show
14 hours agoThe Lou Holtz Show S2 Ep 2 | Chad Hennings on Super Bowls, Fighter Jets, and Leadership #podcast
6K1 -
36:04
Degenerate Plays
16 hours ago $2.13 earnedWhat Movies Would You Bring To A Deserted Island? - Stellar Blade : Part 38
27.1K1 -
29:30
PMG
20 hours ago $0.65 earnedHannah Faulkner and Corinne Cliford | WILDFIRES, FEMA, & GAVIN NEWSOM
15.9K1 -
2:52:22
Alex Zedra
11 hours agoLIVE! New Game | Infestation Origins
37.5K2 -
1:01:25
Rob Braxman Tech
17 hours agoBusy Week in the AI World! What this Means for You!
76.9K22 -
1:02:53
The Charlie Kirk Show
11 hours agoTHOUGHTCRIME Ep. 71 — Airline DEI Again! Fed Redditors? Gayest Movie Ever?
122K88