Premium Only Content
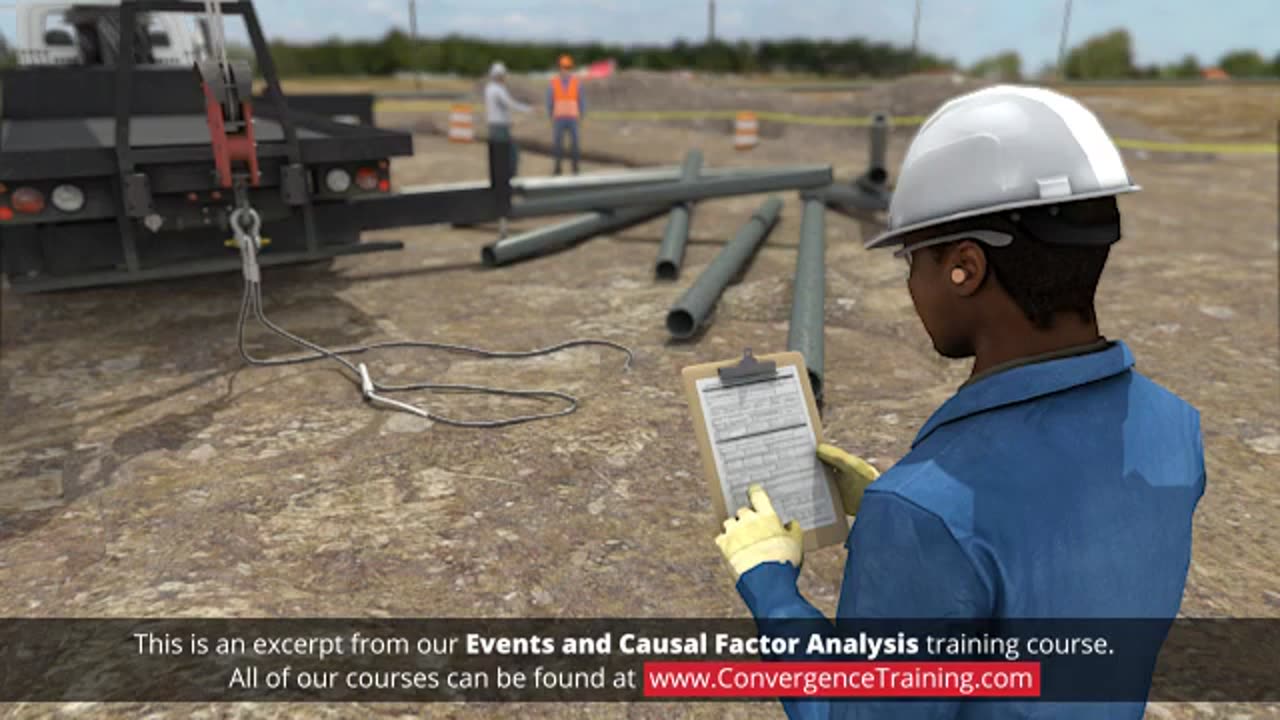
Events and Causal Factor Analysis
**Events and Causal Factor Analysis (ECFA)** is a structured method used to investigate and understand the sequence of events and their contributing causes leading to an incident, failure, or problem. It is commonly used in industries like engineering, healthcare, and aviation to identify root causes and prevent recurrence. Here’s a guide to conducting an ECFA:
---
### **Steps to Conduct an Events and Causal Factor Analysis**
#### 1. **Define the Problem or Incident**
- Clearly state the event or issue being analyzed.
- Include details such as when, where, and how the problem occurred.
- Example: "Equipment malfunction in assembly line #3 on [date]."
---
#### 2. **Gather Data**
- Collect all relevant information related to the event, including:
- Incident reports
- Interview data from witnesses or personnel involved
- Logs, records, or performance metrics
- Photographs, video recordings, or physical evidence
- Ensure accuracy by cross-referencing data from multiple sources.
---
#### 3. **Identify the Timeline**
- Reconstruct the sequence of events leading to the incident.
- **Start with the initiating event** and document all subsequent actions, conditions, and outcomes.
- Use a **chronological order** to ensure clarity.
---
#### 4. **Map the Events**
- Create an **Events and Causal Factors Chart**:
- **Events**: Represent what happened (actions, conditions, or occurrences).
- **Causal Factors**: Represent why it happened (causes, contributing conditions, or failures).
- Use symbols (e.g., rectangles for events, ovals for causal factors) to distinguish between different elements.
- Add arrows to show relationships and dependencies.
Example:
```
Event 1 → Event 2 → Incident
↑
Causal Factor
```
---
#### 5. **Analyze the Causes**
- **Identify Root Causes**: Determine the underlying factors that initiated or contributed to the sequence of events.
- Consider:
- **Human Factors**: Training, communication, fatigue, or error
- **Technical Factors**: Equipment failure, design flaws, or maintenance issues
- **Environmental Factors**: Weather conditions, physical layout, or external pressures
- **Organizational Factors**: Policies, culture, or resource limitations
- Use tools like:
- **5 Whys Analysis**: Repeatedly ask "Why?" to uncover root causes.
- **Fishbone Diagrams**: Categorize and visualize contributing factors.
---
#### 6. **Validate Findings**
- Cross-check findings with data and witness accounts.
- Ensure logical consistency in the causal chain and relationships between events.
---
#### 7. **Develop Recommendations**
- Propose corrective actions to address root causes and prevent recurrence.
- Ensure recommendations are specific, actionable, and measurable.
- Examples:
- Update maintenance schedules.
- Provide additional training for personnel.
- Redesign faulty components or processes.
---
#### 8. **Document and Communicate the Analysis**
- Create a clear and comprehensive report, including:
- Summary of the incident and timeline of events
- Identified causal factors and root causes
- Recommendations and action plans
- Use charts or diagrams to visually communicate findings.
---
#### 9. **Implement and Monitor Corrective Actions**
- Ensure recommended changes are implemented effectively.
- Monitor outcomes and adjust strategies if needed to ensure long-term prevention.
---
### **Key Benefits of ECFA**
- Provides a structured approach to identifying causes.
- Highlights interdependencies between events and contributing factors.
- Promotes organizational learning and prevention of similar incidents.
Would you like to create an ECFA chart or explore specific examples?
-
12:42
Cooking with Gruel
20 hours agoBrown Butter Trifle with Salted Caramel and Cinnamon Apple
10.1K3 -
2:46
BIG NEM
8 hours agoDiscovering RAKIJA: The Holy Liquer of the Balkans
8.05K2 -
1:11:38
Film Threat
13 hours agoCHRISTMAS DAY CHILL STREAM WITH CHRIS GORE | Hollywood on the Rocks
131K24 -
14:22:40
The Quartering
1 day agoYule Log Christmas MAGA Edition With Memes! Come Hang Out!
221K29 -
38:41
MYLUNCHBREAK CHANNEL PAGE
1 day agoTimeline Begins in 1800? - Pt 1 & 2
101K56 -
1:23:41
Game On!
1 day ago $13.48 earnedNetflix NFL Christmas Games Preview and Predictions!
89.4K12 -
2:05:07
Darkhorse Podcast
1 day agoWhy Trump Wants Greenland: The 257th Evolutionary Lens with Bret Weinstein and Heather Heying
318K863 -
8:50:58
Right Side Broadcasting Network
1 day ago🎅 LIVE: Tracking Santa on Christmas Eve 2024 NORAD Santa Tracker 🎅
416K65 -
2:48
Steven Crowder
1 day agoCROWDER CLASSICS: What’s This? | Nightmare Before Kwanzaa (Nightmare Before Christmas Parody)
365K13 -
33:49
Quite Frankly
1 day agoThe Christmas Eve Midnight Telethon
150K30