Premium Only Content
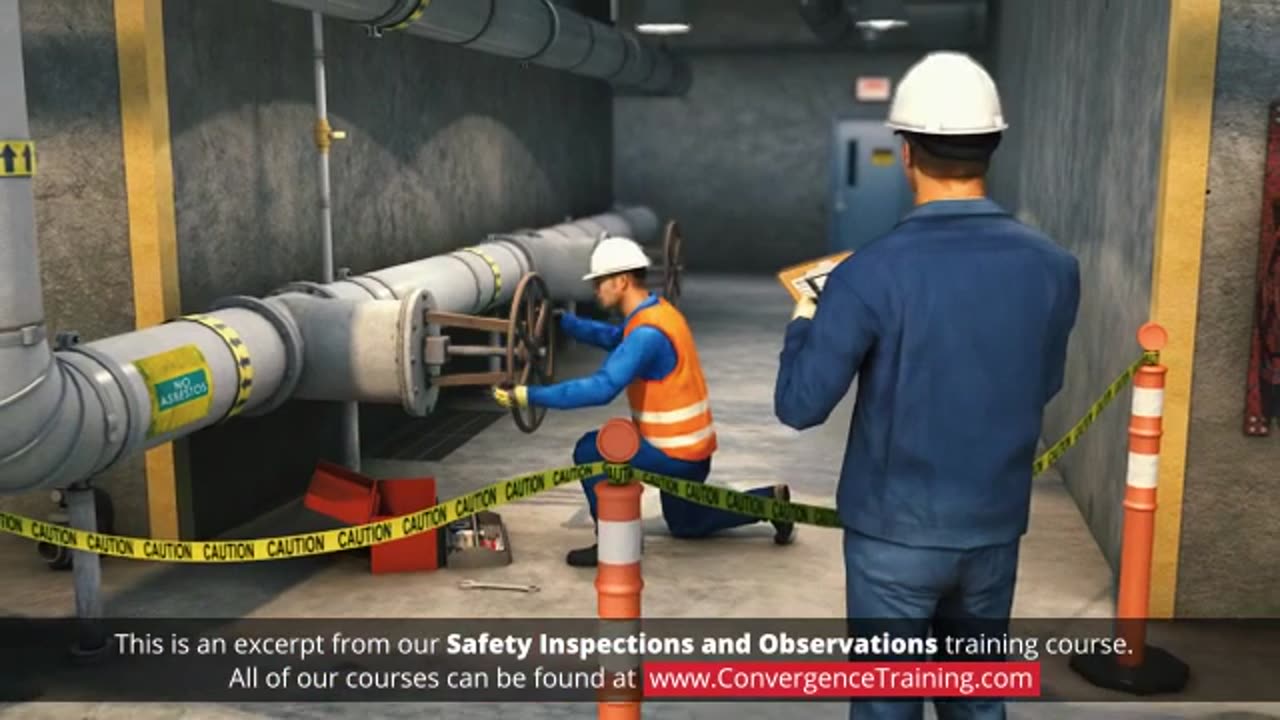
Safety Inspections and Observations
### **Safety Inspections and Observations**
**Safety inspections** and **observations** are proactive processes used to identify, correct, and prevent workplace hazards. They ensure compliance with safety regulations and promote a culture of safety in the workplace.
---
### **What Are Safety Inspections and Observations?**
- **Safety Inspections**: Formal, scheduled evaluations of workplaces, equipment, or processes to identify hazards, unsafe conditions, or regulatory non-compliance.
- **Safety Observations**: Informal, often unscheduled, real-time observations of employee behaviors and work practices to identify unsafe actions or good practices.
Both tools are critical for **continuous improvement** in workplace safety.
---
### **Purpose of Safety Inspections and Observations**
- Identify **hazards** before they lead to incidents.
- Ensure compliance with **safety standards** and regulations (e.g., OSHA).
- Evaluate the condition of **equipment**, processes, and work environments.
- Assess employee adherence to **safe work practices**.
- Reinforce positive behaviors and correct unsafe actions.
- Reduce workplace incidents, injuries, and downtime.
---
### **Types of Safety Inspections**
1. **Routine Inspections**: Regularly scheduled inspections of equipment, tools, and work areas.
2. **Special Inspections**: Conducted after an incident, near-miss, or changes in work processes.
3. **Regulatory Inspections**: Performed to meet legal or compliance requirements.
4. **Pre-Operational Inspections**: Assess equipment or areas before work begins.
5. **Equipment Inspections**: Focus on machinery, vehicles, or tools to ensure proper operation.
---
### **Steps for Conducting Safety Inspections**
1. **Plan the Inspection**:
- Schedule the inspection.
- Determine the scope (e.g., equipment, area, work practices).
- Gather necessary checklists, tools, and standards.
2. **Conduct the Inspection**:
- Use a systematic approach (e.g., left-to-right, top-to-bottom).
- Document hazards, unsafe conditions, or compliance gaps.
- Take photos or videos for evidence when necessary.
- Talk to employees to understand processes and concerns.
3. **Identify and Prioritize Hazards**:
- Use a risk matrix to prioritize hazards based on **severity** and **likelihood**.
- Classify hazards as:
- **Critical**: Immediate action needed.
- **Major**: Action required soon.
- **Minor**: Monitor and address as needed.
4. **Report Findings**:
- Create a clear report summarizing:
- Hazards identified
- Recommendations for corrective actions
- Responsible persons and deadlines
- Share the report with relevant stakeholders (e.g., management, safety committees).
5. **Implement Corrective Actions**:
- Address hazards promptly based on their priority.
- Assign responsibilities for follow-up.
6. **Follow-Up and Verify**:
- Verify corrective actions are completed.
- Reinspect areas or equipment to ensure issues are resolved.
- Track progress using safety reports or software tools.
---
### **Safety Observations Process**
1. **Plan the Observation**:
- Focus on high-risk tasks, areas, or behaviors.
- Decide whether observations will be announced or unannounced.
2. **Observe and Document**:
- Watch employees perform tasks.
- Take note of **safe** and **unsafe behaviors**.
- Avoid interfering with the work unless immediate danger is observed.
3. **Engage with Employees**:
- Provide **positive feedback** for safe behaviors.
- Discuss any unsafe actions in a constructive, non-punitive way.
- Ask for employee input on how to improve safety.
4. **Report and Address Findings**:
- Record observations, both positive and negative.
- Use data to identify trends and implement corrective actions.
5. **Track Behavior Changes**:
- Reobserve over time to verify improvements.
- Recognize and reinforce ongoing safe practices.
---
### **Tools and Checklists for Inspections and Observations**
- **Safety Inspection Checklists**: Customized to workplace needs (e.g., fire safety, PPE compliance, machinery checks).
- **Observation Forms**: Structured forms to record behaviors and conditions.
- **Mobile Apps or Software**: Tools like iAuditor, SafetyCulture, or digital checklists improve efficiency and documentation.
- **Risk Matrix**: To prioritize hazards based on their severity and likelihood.
---
### **Common Areas for Safety Inspections**
1. **Work Areas**:
- Floors, walkways, and exits.
- Housekeeping and clutter.
2. **Equipment and Tools**:
- Machine guards, tools, and power sources.
- Pre-use inspections for forklifts, ladders, or vehicles.
3. **PPE Compliance**:
- Proper use and condition of Personal Protective Equipment (PPE).
4. **Fire Safety**:
- Extinguishers, alarms, and evacuation routes.
5. **Hazardous Materials**:
- Storage, labeling, and handling procedures.
---
### **Benefits of Safety Inspections and Observations**
- Identify hazards early and prevent accidents.
- Promote a **positive safety culture**.
- Ensure compliance with safety regulations.
- Boost employee morale and participation.
- Provide data for continuous safety improvements.
---
### **Best Practices**
1. Combine **inspections** and **observations** for a comprehensive safety approach.
2. Use a **team approach** for inspections to gather diverse perspectives.
3. Train employees to identify hazards and perform informal safety observations.
4. Address hazards promptly and share progress with employees.
5. Recognize safe behaviors to encourage a proactive safety mindset.
---
Would you like help creating a **custom inspection checklist**, designing an **observation form**, or implementing a tracking system for corrective actions? Let me know!
-
3:56:27
Due Dissidence
19 hours agoNewsom ROASTED For Pod Save Interview, Candace Owens CALLS OUT Elon, Ian Carroll RATIOES Israel Post
71.9K52 -
2:16:17
TheSaltyCracker
10 hours agoLooters Descend on LA ReeEEeE Stream 01-12-25
143K302 -
40:32
Man in America
15 hours agoRockefeller Medicine COLLAPSES as God's Natural Healing Takes Over w/ Angie Tomky
50.8K18 -
2:03:30
Nerdrotic
12 hours ago $6.91 earnedMysteries of Egypt with The Brothers of the Serpent | Forbidden Frontier #087
52.7K3 -
2:29:27
vivafrei
20 hours agoEp. 245: Los Angeles ON FIRE! Gavin Newsom FOR JAIL? Trump SENTENCED! Pardons & MORE! VIva & Barnes
203K312 -
5:32:42
Nobodies Live
11 hours ago $5.92 earnedNobodiesLive - Rumble Music TEST STREAM 2.0
67.3K2 -
3:40:10
EricJohnPizzaArtist
10 hours agoAwesome Sauce PIZZA ART LIVE Ep. #30: Classic Gaming!
46.8K7 -
1:18:42
Josh Pate's College Football Show
12 hours ago $0.95 earnedSEC Dominance Over | National Title Thoughts | Miami QB & DC Moves | Wrong About the Playoff?
36.5K4 -
LIVE
Vigilant News Network
16 hours agoIvermectin & Fenbendazole Cancer Secrets Revealed w/ Dr. William Makis | Media Blackout
928 watching -
4:17:11
GamerGril
14 hours agoPRACTICE THOSE DROP KICKS | DEAD ISLAND 2
67K11