Premium Only Content
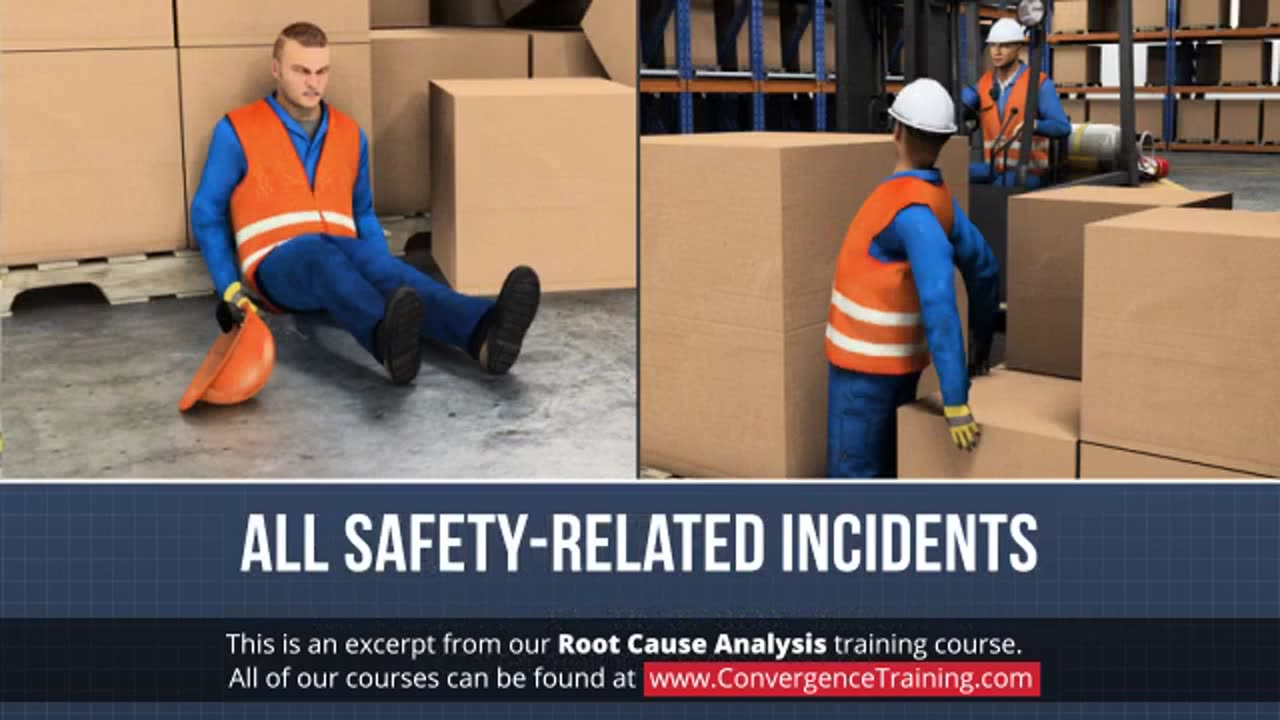
Root Cause Analysis (RCA)
### **Root Cause Analysis (RCA)**
**Root Cause Analysis (RCA)** is a systematic process used to identify the **underlying causes** of an incident, problem, or failure to prevent recurrence. It is widely applied across industries, including manufacturing, healthcare, education, and safety management.
---
### **Purpose of RCA**
- Identify the **root cause(s)** of a problem, not just its symptoms.
- Prevent the issue from recurring.
- Improve processes and systems for long-term solutions.
---
### **When to Use RCA**
RCA is conducted when:
- A **safety incident** or accident occurs.
- Equipment or process **failure** causes downtime.
- **Repetitive issues** occur despite corrective actions.
- Quality control identifies **non-conformances**.
---
### **The RCA Process**
The RCA process typically follows these **5 key steps**:
#### **1. Define the Problem**
- Clearly describe **what happened**, when, and where.
- Gather evidence, including:
- Incident reports
- Interviews with those involved
- Data logs or records
**Example**: *"A machine failure occurred at 10 AM, stopping production for 2 hours."*
---
#### **2. Collect and Analyze Data**
- Gather **quantitative and qualitative data** relevant to the problem.
- Review timelines, processes, and systems.
- Identify contributing factors:
- **Human errors**
- **Equipment malfunctions**
- **Procedural gaps**
---
#### **3. Identify Root Causes**
Use RCA tools to determine the root cause(s):
- **5 Whys Analysis**:
- Ask “Why?” repeatedly (usually 5 times) to drill down to the root cause.
- **Example**:
1. *Why did the machine stop?* → The motor overheated.
2. *Why did the motor overheat?* → The cooling fan failed.
3. *Why did the cooling fan fail?* → It wasn’t maintained.
4. *Why wasn’t it maintained?* → Maintenance schedule was missed.
5. *Why was the schedule missed?* → Staff shortages led to delays.
- **Fishbone Diagram (Ishikawa)**:
- Categorize causes into key areas:
- **People** (training, human error)
- **Processes** (procedures, workflow)
- **Equipment** (breakdowns, wear-and-tear)
- **Environment** (temperature, lighting)
- **Materials** (quality issues, shortages)
- **Failure Mode and Effects Analysis (FMEA)**:
- Assess all failure points in a system and their impact.
---
#### **4. Implement Corrective Actions**
- Develop solutions targeting the **root cause(s)**.
- Implement **corrective and preventive actions (CAPA)**.
- Ensure actions are **specific**, **measurable**, and **realistic**.
**Example**:
- Root Cause: Missed maintenance schedule due to staff shortage.
- Corrective Action: Implement a digital maintenance tracker and cross-train employees.
---
#### **5. Monitor and Verify Results**
- Track the effectiveness of corrective actions.
- Use metrics and key performance indicators (KPIs) to verify improvement.
- Conduct regular follow-ups to ensure issues do not recur.
**Example**: Review monthly maintenance logs to confirm tasks are completed.
---
### **RCA Tools and Techniques**
1. **5 Whys Analysis**
2. **Fishbone Diagram (Ishikawa)**
3. **Pareto Analysis** (80/20 Rule): Identify the most significant problems.
4. **Fault Tree Analysis (FTA)**: Logical diagrams to map causes of failure.
5. **Flowcharts**: Visualize process steps to find breakdowns.
---
### **Benefits of RCA**
- Prevents recurring problems.
- Reduces costs related to downtime, repairs, or safety incidents.
- Enhances **workplace safety** and quality.
- Improves processes and overall efficiency.
---
### **Common RCA Mistakes**
- Stopping at **symptoms** instead of root causes.
- Failing to gather sufficient data.
- Not involving all relevant stakeholders.
- Implementing quick fixes instead of long-term solutions.
---
### **RCA Example Scenario**
**Incident**: A worker slips and falls in a warehouse.
1. **Define the Problem**: Worker fell at Location A at 8 AM.
2. **Collect Data**: Wet floor, poor lighting, no signage.
3. **Identify Root Cause**:
- **Why?** Wet floor.
- **Why?** Water leaked from equipment.
- **Why?** Routine inspections weren’t conducted.
4. **Corrective Actions**:
- Fix equipment leak.
- Conduct regular inspections.
- Improve lighting and add “Wet Floor” signs.
5. **Verify Results**: Monitor for future leaks and ensure inspections occur.
---
Would you like further details on implementing RCA in your organization or a template for specific tools like the **Fishbone Diagram** or **5 Whys Analysis**? Let me know!
-
3:56:27
Due Dissidence
18 hours agoNewsom ROASTED For Pod Save Interview, Candace Owens CALLS OUT Elon, Ian Carroll RATIOES Israel Post
71.9K52 -
2:16:17
TheSaltyCracker
10 hours agoLooters Descend on LA ReeEEeE Stream 01-12-25
143K302 -
40:32
Man in America
15 hours agoRockefeller Medicine COLLAPSES as God's Natural Healing Takes Over w/ Angie Tomky
50.8K18 -
2:03:30
Nerdrotic
12 hours ago $6.91 earnedMysteries of Egypt with The Brothers of the Serpent | Forbidden Frontier #087
52.7K3 -
2:29:27
vivafrei
20 hours agoEp. 245: Los Angeles ON FIRE! Gavin Newsom FOR JAIL? Trump SENTENCED! Pardons & MORE! VIva & Barnes
203K312 -
5:32:42
Nobodies Live
11 hours ago $5.92 earnedNobodiesLive - Rumble Music TEST STREAM 2.0
67.3K2 -
3:40:10
EricJohnPizzaArtist
10 hours agoAwesome Sauce PIZZA ART LIVE Ep. #30: Classic Gaming!
46.8K7 -
1:18:42
Josh Pate's College Football Show
12 hours ago $0.95 earnedSEC Dominance Over | National Title Thoughts | Miami QB & DC Moves | Wrong About the Playoff?
36.5K4 -
LIVE
Vigilant News Network
16 hours agoIvermectin & Fenbendazole Cancer Secrets Revealed w/ Dr. William Makis | Media Blackout
920 watching -
4:17:11
GamerGril
14 hours agoPRACTICE THOSE DROP KICKS | DEAD ISLAND 2
67K11