Premium Only Content
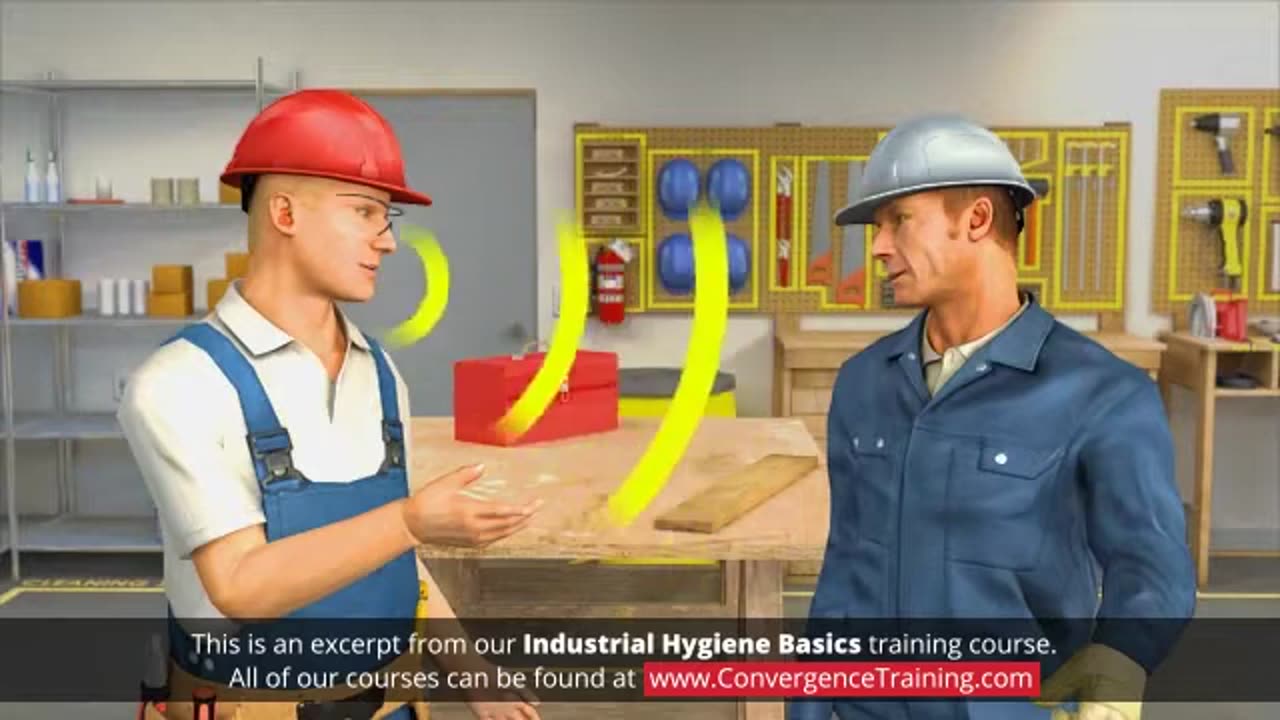
Industrial Hygiene Basics Training
### **Industrial Hygiene Basics Training Guide**
**Objective**: Educate employees and supervisors on the principles of industrial hygiene, the identification of workplace hazards, and how to implement controls to ensure health and safety.
---
### **1. What is Industrial Hygiene?**
- **Definition**:
Industrial hygiene is the science of recognizing, evaluating, and controlling workplace hazards that may cause illness or injury.
- **Primary Goal**:
Protect workers’ health by minimizing exposure to harmful agents and environments.
---
### **2. Key Workplace Hazards**
Industrial hygiene focuses on five main types of hazards:
#### **1. Chemical Hazards**
- Examples: Solvents, gases, vapors, fumes, dust, and mists.
- Exposure Routes: Inhalation, skin contact, ingestion, or injection.
#### **2. Physical Hazards**
- Examples: Noise, vibration, extreme temperatures, radiation (ionizing and non-ionizing).
- Effects: Hearing loss, burns, or other physical injuries.
#### **3. Biological Hazards**
- Examples: Viruses, bacteria, fungi, mold, and bloodborne pathogens.
- Sources: Healthcare settings, laboratories, or areas with stagnant water.
#### **4. Ergonomic Hazards**
- Examples: Poor workstation design, repetitive motion, lifting, or awkward postures.
- Effects: Musculoskeletal disorders (MSDs), such as carpal tunnel syndrome or back injuries.
#### **5. Environmental Hazards**
- Examples: Poor ventilation, excessive humidity, or inadequate lighting.
- Effects: Respiratory issues or reduced productivity.
---
### **3. Core Principles of Industrial Hygiene**
#### **1. Anticipation**
- Predict potential hazards during planning stages of operations or processes.
#### **2. Recognition**
- Identify existing hazards in the workplace through observation, employee feedback, and job hazard analyses.
#### **3. Evaluation**
- Measure the extent of exposure using air sampling, noise monitoring, and other methods.
- Compare results to established standards (e.g., OSHA Permissible Exposure Limits (PELs)).
#### **4. Control**
- Implement strategies to reduce or eliminate hazards using the **Hierarchy of Controls**:
1. **Elimination**: Remove the hazard entirely.
2. **Substitution**: Replace hazardous materials or processes with safer alternatives.
3. **Engineering Controls**: Use ventilation systems, sound barriers, or safety guards.
4. **Administrative Controls**: Implement training, shift rotations, or standard operating procedures (SOPs).
5. **Personal Protective Equipment (PPE)**: Use respirators, gloves, goggles, and hearing protection.
---
### **4. Role of the Industrial Hygienist**
- Conduct workplace assessments to identify hazards.
- Recommend control measures and ensure regulatory compliance.
- Train employees and monitor the effectiveness of control measures.
---
### **5. Monitoring and Sampling**
- **Air Sampling**: Measure concentrations of airborne chemicals or particulates.
- **Noise Monitoring**: Use sound level meters or dosimeters to assess noise exposure.
- **Heat Stress Monitoring**: Measure temperature, humidity, and physical workload.
---
### **6. Workplace Controls**
#### **Engineering Controls**
- Examples:
- Fume hoods for chemical exposure.
- Sound-dampening enclosures for noisy machinery.
- Ventilation systems for improved air quality.
#### **Administrative Controls**
- Rotate workers to reduce exposure duration.
- Schedule high-exposure tasks during off-peak hours.
- Provide regular safety training and updates.
#### **PPE**
- Use PPE as a last resort or in conjunction with other controls.
- Ensure proper selection, fitting, and maintenance of equipment.
---
### **7. Health Effects of Workplace Exposures**
- **Acute Effects**: Symptoms appear quickly, such as dizziness, burns, or allergic reactions.
- **Chronic Effects**: Develop over time, such as cancer, hearing loss, or respiratory diseases.
---
### **8. Training and Employee Involvement**
- **Training Topics**:
- Hazard communication (HazCom) and Safety Data Sheets (SDS).
- Proper use and maintenance of PPE.
- Emergency response procedures.
- **Employee Role**:
- Report hazards or unsafe conditions to supervisors.
- Follow established safety procedures.
- Participate in training and inspections.
---
### **9. Regulatory Framework**
- **OSHA Standards**:
- Hazard Communication Standard (29 CFR 1910.1200).
- Respiratory Protection Standard (29 CFR 1910.134).
- Occupational Noise Exposure (29 CFR 1910.95).
- **Other Standards**:
- American Conference of Governmental Industrial Hygienists (ACGIH) Threshold Limit Values (TLVs).
- National Institute for Occupational Safety and Health (NIOSH) guidelines.
---
### **10. Emergency Preparedness**
- Develop response plans for hazardous material spills, fires, or exposure incidents.
- Maintain first aid kits and emergency showers/eyewash stations.
- Train employees in spill containment and evacuation procedures.
---
### **11. Evaluating and Improving the Program**
- Conduct regular audits and risk assessments.
- Use feedback from employees and monitoring data to refine controls.
- Stay updated on new regulations and technologies in industrial hygiene.
---
Would you like this information formatted as a presentation, checklist, or detailed guide? I can also include industry-specific examples or templates for hazard evaluations and monitoring logs.
-
6:43
HSESafetyInformation
2 months agoLahori Chanay Recipe - Lahori Cholay Recipe - Chana Chana Masala
39 -
10:50
SKAP ATTACK
18 hours ago $0.29 earnedNico Harrison is a Disgrace
4.91K8 -
18:13
Bearing
16 hours agoMy Girlfriend is a DOG 🐶🦴😳
11.6K36 -
25:56
This Bahamian Gyal
12 hours agoBOTCHED: The WORST Plastic Surgeries Ever! | This Bahamian Gyal
5.97K3 -
37:25
Uncommon Sense In Current Times
15 hours ago $0.34 earnedFaith-Based Films Are Rising—And Hollywood Can’t Ignore It | Greg Rabidoux
12.5K -
11:14
unclemattscookerylessons
22 hours ago $0.16 earnedRoast beef and yorkshire pudding
5.86K7 -
2:46:10
TimcastIRL
10 hours agoTim Pool & Crew CRASH White House Press Briefing And Liberal Media IS PISSED | Timcast IRL
247K161 -
2:49:19
Laura Loomer
10 hours agoEP116: COUP DE SANTIS: FL Legislators Investigate Ron And Casey For Fraud
87.9K62 -
8:00:00
SpartakusLIVE
16 hours ago$50,000 Tourney w/ ZLANER & Oak! || MORE WZ to follow
41.3K5 -
1:51:14
FreshandFit
2 days agoUniversity Of South Carolina Speech
124K42