Premium Only Content
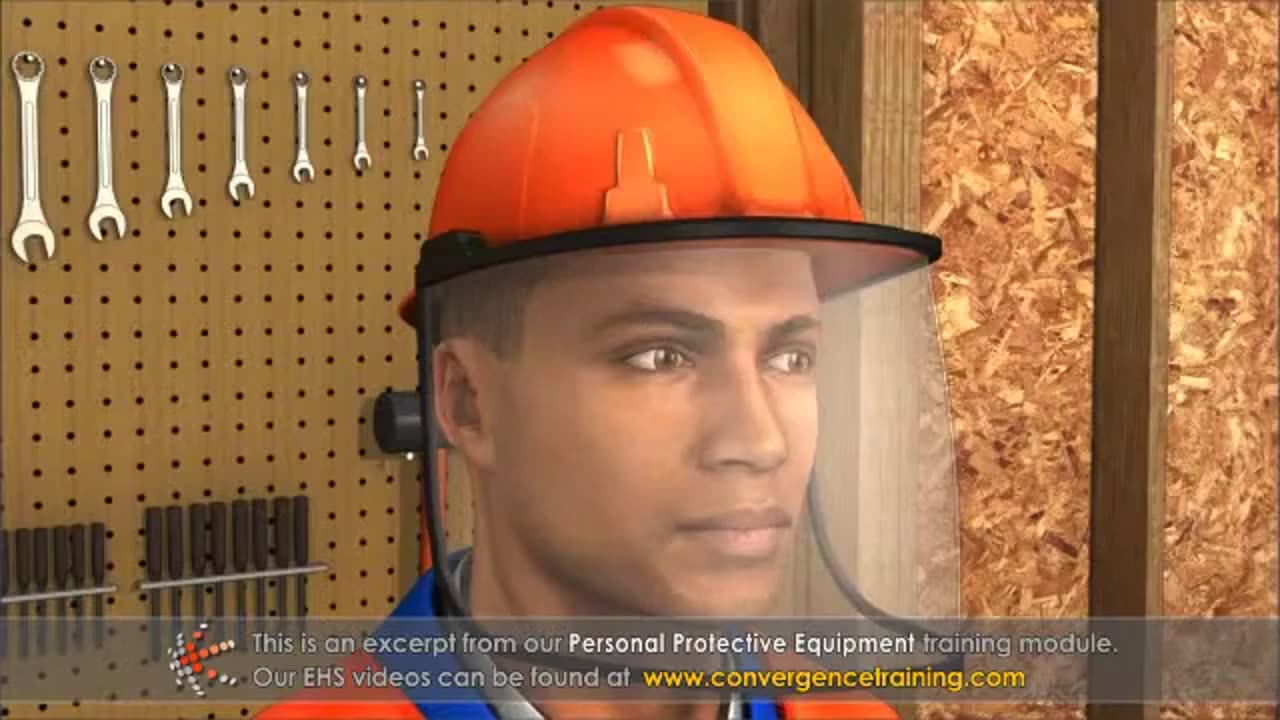
Personal Protective Equipment (PPE) Training
**Personal Protective Equipment (PPE) Training** is essential for ensuring that workers understand the importance of PPE and how to correctly use, maintain, and dispose of it. PPE is designed to protect employees from workplace hazards that cannot be eliminated through engineering controls, administrative controls, or other safety measures. This training equips workers with the knowledge and skills to protect themselves from injury or illness while performing their tasks.
### **Key Components of Personal Protective Equipment (PPE) Training**
#### 1. **Introduction to PPE**
- **Definition of PPE**: PPE refers to protective clothing, helmets, goggles, gloves, or other equipment designed to protect the wearer from injury or infection.
- **Types of Hazards Addressed by PPE**:
- **Physical Hazards**: Mechanical injuries (e.g., cuts, abrasions), thermal hazards (e.g., heat or cold), and radiation.
- **Chemical Hazards**: Exposure to harmful chemicals through skin contact, inhalation, or eye exposure.
- **Biological Hazards**: Contamination by pathogens or infectious materials.
- **Electrical Hazards**: Risks of electric shock or arc flash.
#### 2. **Why PPE is Important**
- **Protects Workers**: PPE acts as the last line of defense when engineering and administrative controls are not enough to mitigate risks.
- **Reduces Injuries and Illnesses**: Proper use of PPE helps prevent accidents and reduces the severity of injuries in hazardous environments.
- **Compliance with Regulations**: OSHA (Occupational Safety and Health Administration) and other regulatory bodies require the use of appropriate PPE in certain work environments to ensure employee safety.
#### 3. **Types of Personal Protective Equipment**
PPE comes in various forms, each designed to protect against specific risks. Some common types of PPE include:
- **Head Protection**:
- **Hard Hats**: Protect against falling objects, impacts, and head injuries in construction, manufacturing, and other environments.
- **Eye and Face Protection**:
- **Safety Glasses**: Shield eyes from flying particles, dust, or chemical splashes.
- **Goggles**: Provide more complete coverage than safety glasses and are often used in environments with hazardous chemicals or in laboratory settings.
- **Face Shields**: Used for facial protection against chemicals, impacts, or extreme heat.
- **Hearing Protection**:
- **Earplugs**: Inserted into the ear canal to reduce noise exposure.
- **Earmuffs**: Cover the entire outer ear and provide better noise reduction, especially in high-noise environments.
- **Respiratory Protection**:
- **Dust Masks**: Protect from inhaling dust and particulate matter.
- **Respirators**: Protect against harmful airborne contaminants such as chemicals, gases, or vapors.
- **Hand and Arm Protection**:
- **Gloves**: Used to protect against cuts, burns, chemical exposure, or electrical hazards. Different types of gloves are designed for specific tasks (e.g., rubber gloves for chemicals, leather gloves for handling rough materials).
- **Sleeves**: Can be used to protect arms from cuts, burns, or chemical exposure.
- **Foot and Leg Protection**:
- **Safety Boots/Shoes**: Designed to protect feet from crushing, punctures, slips, or electrical hazards. Steel-toed boots are commonly used in construction and manufacturing.
- **Leggings or Chaps**: Protect legs from exposure to sharp objects, chemicals, or fire.
- **Body Protection**:
- **Aprons**: Protect the body from cuts, burns, or chemical splashes.
- **Coveralls**: Provide full-body protection from dust, chemicals, or contamination.
- **Flame-Resistant Clothing**: Protect workers from burns and injuries caused by flash fires or high heat environments.
- **Fall Protection**:
- **Harnesses and Lanyards**: Used in situations where workers are at risk of falling from heights (e.g., construction, maintenance).
- **Guardrails and Safety Nets**: Provide physical barriers to prevent falls.
#### 4. **PPE Selection**
- **Risk Assessment**: A proper risk assessment is necessary to determine the type of PPE required for each task or work environment. Factors such as the nature of the hazard, the severity of potential injury, and the duration of exposure must be considered.
- **PPE Matching**: PPE should be matched to the specific hazard it is designed to protect against. For example, chemical-resistant gloves should be selected when handling hazardous substances, and ear protection should be worn in loud environments.
- **Comfort and Fit**: PPE must fit properly to be effective. Ill-fitting PPE can compromise safety, leading to potential injury or discomfort.
#### 5. **Proper Use of PPE**
- **Donning (Putting On) PPE**:
- Ensure the PPE is clean and free from damage.
- Use the correct method for donning PPE, following manufacturer instructions and safety guidelines.
- Make sure all straps, seals, and fasteners are secure and comfortable.
- **Doffing (Taking Off) PPE**:
- Remove PPE in the correct order to avoid contamination or exposure to hazardous materials.
- For example, when removing gloves, remove them from the inside out to avoid contact with the outer surface that may be contaminated.
- Avoid touching your face, especially the eyes, nose, or mouth, when removing PPE.
#### 6. **Maintenance and Care of PPE**
- **Inspection**: Regularly inspect PPE for damage, wear, or contamination. PPE that is damaged or worn out should be replaced immediately.
- **Cleaning**: Some PPE, such as gloves, goggles, and coveralls, may need to be cleaned regularly to maintain their effectiveness and longevity. Follow manufacturer instructions for cleaning methods and materials.
- **Storage**: Store PPE in a clean, dry place where it will not be exposed to unnecessary wear or environmental hazards (e.g., sunlight, chemicals).
- **Repairs**: Only authorized personnel should repair PPE, and repairs must be done in accordance with the manufacturer’s guidelines.
#### 7. **Limitations of PPE**
- **PPE is Not a Substitute for Proper Safety Measures**: PPE should be used in conjunction with other safety controls (e.g., engineering controls, administrative controls) and not as the only protective measure.
- **Comfort and Wearability**: While PPE is essential for safety, it can sometimes be uncomfortable. It is important to wear PPE that fits properly and provides adequate protection without causing unnecessary discomfort or restricting movement.
- **Duration of Use**: Extended use of certain PPE, such as respirators or hearing protection, can lead to discomfort. It is essential to take breaks and assess the need for PPE throughout the workday.
#### 8. **PPE Training and Employee Responsibilities**
- **Employee Understanding**: Employees must fully understand the importance of PPE and how to use it correctly. They should know the risks of not wearing PPE and how it can prevent injuries.
- **Employer Responsibilities**: Employers are responsible for providing the appropriate PPE for employees, ensuring that it is in good working condition, and offering training on its proper use and maintenance.
- **Regular Training**: Employees should receive PPE training during onboarding and regularly throughout their employment, especially if they change tasks or work in new environments.
#### 9. **PPE in Emergency Situations**
- **Emergencies**: In case of an emergency, such as a chemical spill, fire, or electrical shock, employees must know how to quickly access and use the necessary PPE.
- **Evacuation and Safety Procedures**: Employees should be trained on evacuation routes, emergency exits, and the correct use of emergency PPE in various scenarios.
#### 10. **Conclusion**
PPE is a vital element of workplace safety, but it is only effective when used properly and in conjunction with other safety measures. Employees must be trained to select, use, maintain, and dispose of PPE correctly to protect themselves from workplace hazards. Regular training and assessments help ensure that employees are always prepared to handle potential risks in a safe and efficient manner. PPE should never be viewed as a substitute for eliminating hazards, but rather as an essential tool for minimizing risk in hazardous environments.
-
12:33
Silver Dragons
2 hours agoSilver Price Crushed Today - NEW TREND STARTING?
2.27K -
1:02:03
In The Litter Box w/ Jewels & Catturd
21 hours agoRecall Newscum & Bass! | In the Litter Box w/ Jewels & Catturd – Ep. 718 – 1/13/2025
38.7K20 -
3:19:58
Tate Speech by Andrew Tate
9 hours agoEMERGENCY MEETING EPISODE 101 - STRENGTH AND HONOR
129K61 -
1:48:09
The Quartering
5 hours agoLA Fires Are About To Get Way Worse, Trump Vs Vance On J6 Pardons, Brett Cooper Bombshell & More
83.1K35 -
LIVE
Dr Disrespect
6 hours ago🔴LIVE - DR DISRESPECT - MARVEL RIVALS - TOP 500 IN THE WORLD
3,066 watching -
1:05:49
MTNTOUGH Fitness Lab
7 hours agoDamon West: How Faith and Mental Toughness Helped Me Escape Prison | MTNPOD #99
6.49K -
1:43:05
The Criminal Connection Podcast
7 hours agoIAN MCCRANOR: World Champion Karate Doorman CRAZY Life Story, Mob Hits GONE WRONG & Video Game Star!
5.58K1 -
38:25
otisframpton
2 hours agoPROCREATE DREAMS Animation Demo - Part 4 - Lighting & SFX!
16.3K -
1:53:53
vivafrei
5 hours agoGavin Newsom's War With Elon! Stolen Humvees FOUND? Arson Suspect IDENTIFIED? Cali Updates & MORE!
72.1K43 -
1:58:10
Nerdrotic
6 hours ago $4.06 earnedReconstructing the Superhero | FNT Square Up - Nerdrotic Nooner 457
59.1K6