Premium Only Content
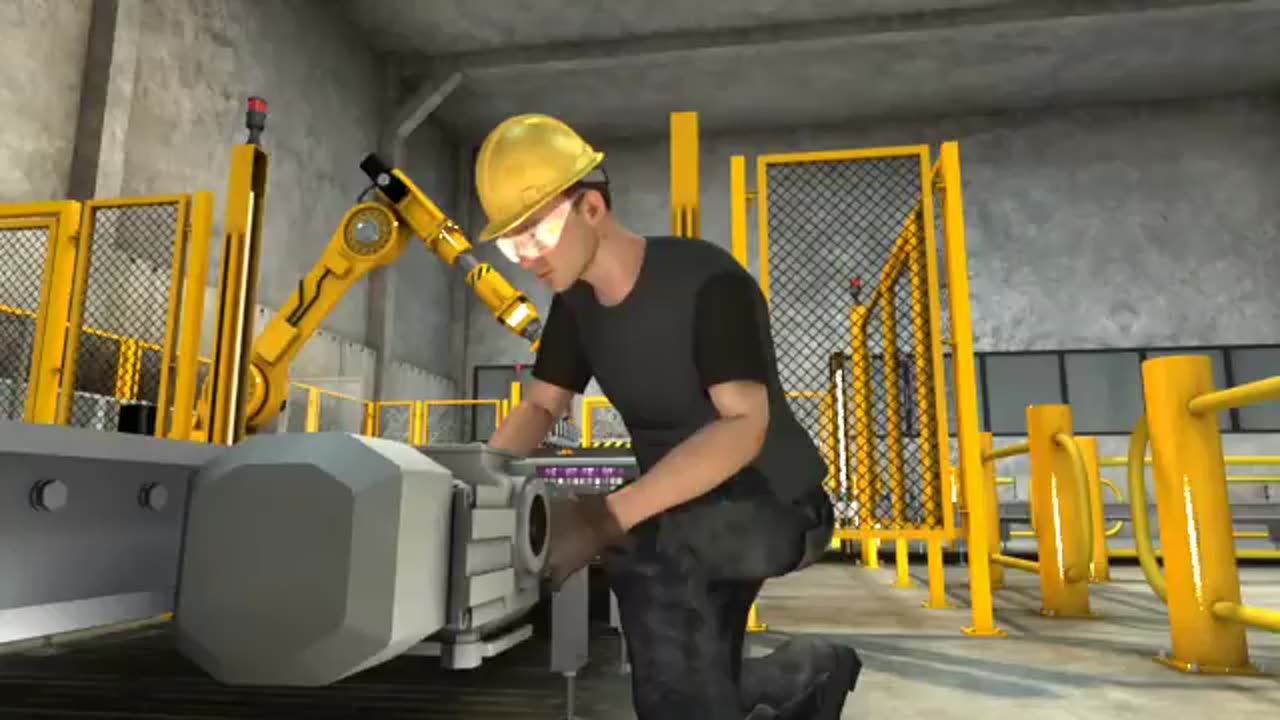
Conveyor Safety Training
Conveyor Safety Training is designed to ensure that workers understand the safe operation, maintenance, and troubleshooting of conveyor systems to prevent accidents and injuries. Conveyor systems are widely used in industries like manufacturing, logistics, and food processing, but they can present significant hazards if not properly managed. Training is crucial for reducing risks and improving the safety of those working around these systems.
### Key Elements of Conveyor Safety Training
#### 1. **Introduction to Conveyor Systems**
- **Types of Conveyors:** Belt conveyors, roller conveyors, chain conveyors, screw conveyors, and more.
- **Components:** Motors, pulleys, belts, rollers, gears, and drives.
- **Common Conveyor Hazards:** Moving parts, pinch points, entanglement, falling objects, electrical hazards, and improper loading.
#### 2. **Identifying Conveyor Hazards**
- **Pinch Points:** Areas where body parts, clothing, or tools could get caught between conveyor parts.
- **Entanglement Risks:** Loose clothing, jewelry, or long hair being caught in moving parts.
- **Falling Objects:** Improperly secured items on the conveyor or when loading/unloading.
- **Electrical Hazards:** Issues related to power supply or equipment malfunction.
- **Slips, Trips, and Falls:** Poor housekeeping and obstructions near conveyor systems.
#### 3. **Safe Operation Procedures**
- **Starting and Stopping Conveyors:** Proper procedures for starting, stopping, and troubleshooting the conveyor system.
- **Safe Loading and Unloading:** Guidelines for loading items onto the conveyor safely to avoid overloading or imbalance.
- **Monitoring Conveyor Systems:** Regular monitoring of conveyor performance for signs of malfunction or damage.
- **Speed Control:** Understanding the risks of running conveyors at excessive speeds.
#### 4. **Lockout/Tagout (LOTO) Procedures**
- **Definition:** Lockout/Tagout is a critical procedure to isolate and de-energize conveyor systems before maintenance.
- **When to Perform LOTO:** Maintenance, cleaning, or adjustments.
- **Steps for Lockout/Tagout:** Shutting off power, isolating energy sources, and applying lockout/tagout devices.
- **Personal Protective Equipment (PPE):** Ensuring employees wear appropriate PPE, such as gloves and safety glasses, when handling conveyors.
#### 5. **Emergency Stop Mechanisms**
- **Location and Activation:** How to quickly stop a conveyor in case of an emergency.
- **Emergency Stop Buttons and Pull Cords:** Training workers to use these systems effectively in critical situations.
#### 6. **Preventive Maintenance and Inspections**
- **Routine Inspections:** Checking for wear, damage, and debris buildup on belts, rollers, and motors.
- **Lubrication:** Maintaining proper lubrication of moving parts to reduce friction and prevent breakdowns.
- **Belts and Pulleys:** Inspecting for alignment issues, tension problems, and wear.
- **Electrical System Checks:** Ensuring all wiring and connections are secure and not exposed to prevent electrical hazards.
#### 7. **Proper Housekeeping Practices**
- **Clean and Clear Pathways:** Keeping the conveyor system area clear of debris, materials, and obstacles.
- **Spill Cleanup:** Cleaning up any material spills immediately to prevent slips or damage to the conveyor.
- **Emergency Access:** Ensuring that aisles and emergency exits around the conveyor system are clear.
#### 8. **Employee Roles and Responsibilities**
- **Operators:** Ensuring conveyors are operated safely, conducting pre-operation checks, and reporting issues.
- **Maintenance Personnel:** Regularly inspecting and maintaining the conveyor system, ensuring that LOTO procedures are followed during repairs.
- **Supervisors/Managers:** Overseeing safety protocols, ensuring that safety training is up-to-date, and enforcing safe work practices.
#### 9. **Training Frequency and Documentation**
- **Initial Training:** Providing comprehensive training for all new employees and those working directly with conveyors.
- **Refresher Training:** Annual or periodic updates to ensure that workers are up-to-date on safety protocols.
- **Documentation:** Maintaining records of training, inspections, and any safety incidents involving conveyors.
### Key Safety Practices for Conveyor Systems
- **Wear PPE:** Depending on the environment, this may include gloves, safety goggles, hearing protection, steel-toed boots, and helmets.
- **Avoid Loose Clothing:** Ensure that workers' clothing is properly secured to prevent entanglement.
- **Do Not Bypass Safety Features:** Conveyors are equipped with safety devices like emergency stops and guards—these should never be bypassed or disabled.
- **Report Hazards Immediately:** Workers should be trained to report malfunctioning or unsafe conditions.
### Benefits of Conveyor Safety Training
- **Prevents Accidents and Injuries:** Proper training reduces the likelihood of accidents such as entanglement, crushing, or falls.
- **Improves Efficiency:** Safe and efficient operation of conveyor systems leads to fewer breakdowns and better productivity.
- **Compliance with Regulations:** Meeting OSHA (Occupational Safety and Health Administration) and other industry standards for workplace safety.
### Training Delivery Methods
- **In-Person Workshops:** Hands-on training in the facility with real conveyor systems.
- **Online Modules:** Convenient for theoretical knowledge, often followed by in-person practical exercises.
- **Job-Specific Training:** Customizing training for specific types of conveyor systems or industries.
If you're planning or organizing conveyor safety training, would you like any specific materials, such as training outlines or resources for specific industries?
-
7:58
HSESafetyInformation
1 month agoAuthentic Peshawari Rosh _ Namkeen Gosht Recipe __ Traditional KPK and Baluchistan
581 -
LIVE
SpartakusLIVE
2 hours ago#1 Action HERO ends your weekend in a FIERY BLAZE of non-stop GLORY
595 watching -
LIVE
The Sufari Hub
1 hour ago🔴ELDEN RING MODDED - ROAD TO #1 GAMER ON RUMBLE - #RumbleGaming
69 watching -
54:47
Sarah Westall
4 hours agoTranshumanism vs Natural Human Zones, AI consciousness and the Hive Mind Future w/ Joe Allen
23.6K5 -
LIVE
Joke65
1 hour ago[LIVE] The Sunday Surprise! | Counter Strike w/ Omega (Meisters Madness)
134 watching -
LIVE
MaverickLIVE
1 hour agoFirst Rumble Stream!
111 watching -
LIVE
xTimsanityx
5 hours ago🟢LIVE: COACH ALWAYS TOLD ME, "SHOOTERS SHOOT" | GOONING ON E-DISTRICT
48 watching -
32:19
SB Mowing
2 days agoThis yard was putting KIDS IN DANGER - Now they can SAFELY play outside again
15.7K21 -
LIVE
Lofi Girl
2 years agolofi hip hop radio 📚 - beats to relax/study to
642 watching -
47:41
Tactical Advisor
5 hours agoMake Your AR15 into a Bullpup/New Thermals | Vault Room Live Stream 018
39.9K12