Premium Only Content
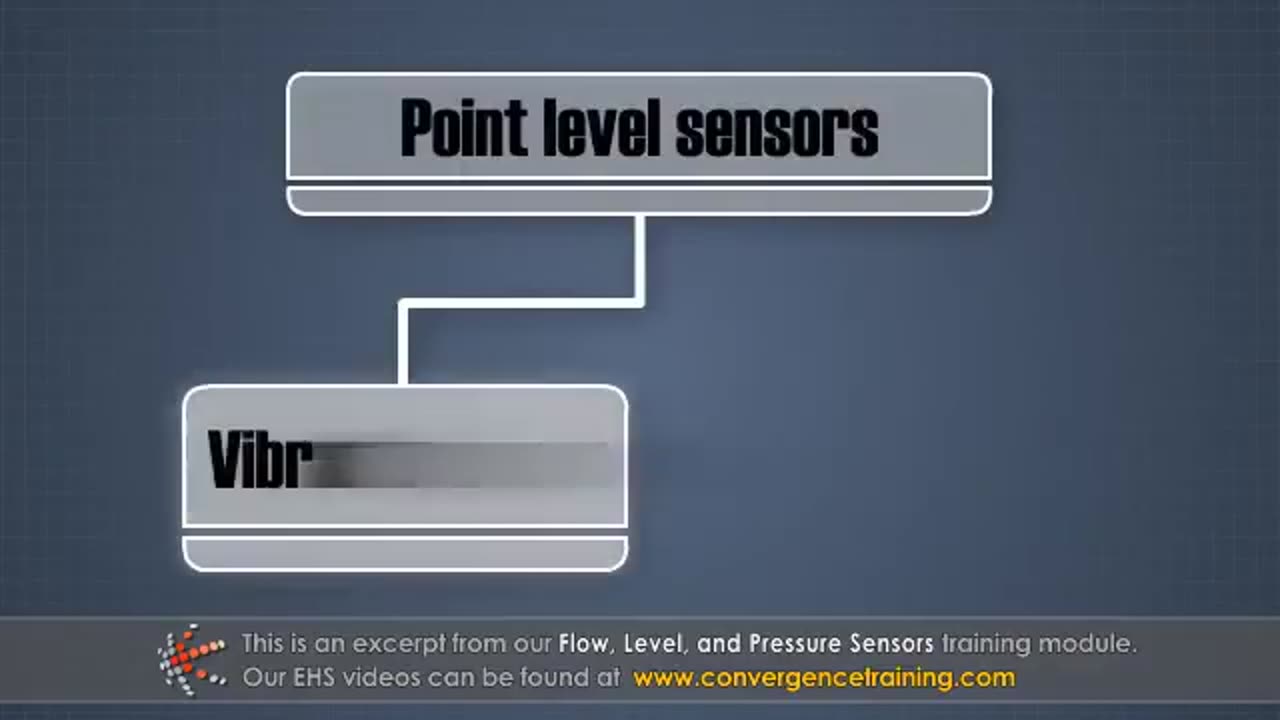
Flow, Level, and Pressure Sensors
### **Flow, Level, and Pressure Sensors: Essential Components in Hydraulic and Industrial Systems**
Sensors play a critical role in monitoring and controlling systems in various industrial applications, including hydraulic, water treatment, chemical, and manufacturing systems. **Flow, level, and pressure sensors** are integral to ensuring system efficiency, safety, and reliability. Here’s an overview of these sensors, their types, and applications:
---
### **1. Flow Sensors (Flow Meters)**
Flow sensors measure the rate of flow of liquids, gases, or slurry within a system. They provide real-time data that helps operators control the flow, prevent overflows, and optimize system performance.
#### **Types of Flow Sensors:**
- **Mechanical Flow Meters:**
- **Turbine Flow Meters:** Use a turbine that rotates as fluid flows through it. The speed of rotation correlates with the flow rate.
- **Paddlewheel Flow Meters:** Employ a rotating paddle to measure the flow. The rotation speed is proportional to the flow rate.
- **Electromagnetic Flow Meters:** Use Faraday’s law of induction to measure the flow of conductive liquids. They do not have moving parts, making them more reliable in many applications.
- **Ultrasonic Flow Meters:** Measure the flow rate using the time-of-flight of ultrasonic sound waves traveling through the fluid. Commonly used for non-invasive flow measurements.
- **Coriolis Flow Meters:** Measure mass flow by detecting changes in vibration caused by the flowing liquid or gas. These are highly accurate but often more expensive.
- **Vortex Flow Meters:** Measure the frequency of vortices shed by a bluff body placed in the flow. The frequency of the vortices is directly proportional to the flow rate.
#### **Applications:**
- **Hydraulic Systems:** Monitor the flow of hydraulic fluid to ensure proper operation and prevent overheating or excessive wear.
- **Water Treatment Plants:** Measure the flow of water through pipes for treatment, distribution, and filtration.
- **Oil and Gas Industry:** Monitor the flow of oil, gas, or chemical fluids through pipelines.
- **HVAC Systems:** Monitor air or water flow in heating and cooling applications.
---
### **2. Level Sensors**
Level sensors detect the level of liquid, slurry, or solid material within a container or vessel. They are used to prevent overflows, manage inventories, and control material flow in tanks, silos, and other storage systems.
#### **Types of Level Sensors:**
- **Float Level Sensors:** Use a buoyant float that rises and falls with the liquid level. The float can trigger a switch or a signal for control purposes.
- **Capacitive Level Sensors:** Measure the change in capacitance caused by the presence of a material. These sensors can detect both liquid and solid materials, including granular materials.
- **Ultrasonic Level Sensors:** Emit sound waves and measure the time it takes for the sound to reflect off the material’s surface. The time delay correlates to the material's level.
- **Radar Level Sensors:** Use microwave radar waves that reflect off the material’s surface to determine the level. These sensors are effective in high-temperature and high-pressure environments.
- **Conductive Level Sensors:** Use electrical conductivity to detect the presence of a material. The sensor is typically made of two electrodes, and when a material (liquid or solid) connects the electrodes, it triggers a response.
- **Optical Level Sensors:** Use light to detect the presence of a material. When the sensor’s light beam is interrupted, it indicates a change in material level.
#### **Applications:**
- **Tanks and Reservoirs:** Measure liquid or slurry levels in storage tanks, ensuring the tank doesn’t overflow or run dry.
- **Industrial Processes:** Monitor levels of raw materials, chemicals, or waste products in manufacturing or treatment processes.
- **Pumps and Boilers:** Help maintain water or fluid levels in systems to prevent damage from low levels or overflow.
- **Food and Beverage Industry:** Ensure the correct filling levels in bottles, cans, or containers during packaging.
---
### **3. Pressure Sensors**
Pressure sensors measure the pressure of gases or liquids within a system. These sensors are critical for monitoring system health, preventing damage due to over-pressurization, and ensuring safe operation.
#### **Types of Pressure Sensors:**
- **Strain Gauge Pressure Sensors:** Use a strain gauge element to detect changes in pressure. The strain gauge measures deformation in a diaphragm, which correlates to the pressure applied to it.
- **Piezoelectric Pressure Sensors:** Use piezoelectric materials that generate an electrical charge in response to pressure. These sensors are highly sensitive and typically used for dynamic pressure measurement.
- **Capacitive Pressure Sensors:** Measure changes in capacitance caused by diaphragm deflection in response to pressure. These sensors offer high accuracy and stability.
- **Bourdon Tube Pressure Sensors:** Use a curved tube that straightens as pressure increases. The deflection is then translated into a pressure reading via a mechanical linkage.
- **Differential Pressure Sensors:** Measure the difference between two pressure points. These are useful for monitoring filters, pumps, or flow rates in a system.
#### **Applications:**
- **Hydraulic Systems:** Monitor fluid pressure to avoid over-pressurization, which can cause damage to pumps, actuators, and hoses.
- **Oil and Gas Industry:** Monitor pipeline pressures to prevent leaks, over-pressurization, and ensure safe transportation of materials.
- **Automotive Industry:** Measure tire pressure, fuel systems, and engine performance for safety and efficiency.
- **HVAC Systems:** Monitor air or refrigerant pressure to ensure efficient heating, ventilation, and air conditioning processes.
- **Water Treatment Systems:** Measure water pressure in pipes and valves to maintain optimal flow rates.
---
### **4. Choosing the Right Sensor for Your Application**
When selecting flow, level, or pressure sensors for an application, consider the following factors:
#### **For Flow Sensors:**
- Type of fluid (viscosity, conductivity, cleanliness)
- Flow range and accuracy requirements
- Sensor response time
- Maintenance and cleaning needs (e.g., electromagnetic flow meters have no moving parts and are low maintenance)
#### **For Level Sensors:**
- Material type (liquid, slurry, or solid)
- Sensitivity to changing conditions (e.g., temperature or pressure)
- Environment (e.g., corrosive, high-temperature, or hazardous)
- Required accuracy and resolution
#### **For Pressure Sensors:**
- Pressure range (high, low, or differential pressure)
- Temperature and environmental conditions
- Material compatibility with fluids or gases
- Type of measurement (static vs. dynamic pressure)
---
### **Conclusion**
Flow, level, and pressure sensors are critical components in a variety of industrial and commercial systems. By selecting the appropriate sensor for each specific application, you can ensure accurate monitoring, optimize system performance, and protect equipment from damage. These sensors are essential in maintaining efficient, safe, and reliable operations in hydraulic, water treatment, manufacturing, and other systems.
-
9:49
Tundra Tactical
9 hours ago $13.14 earnedThe Best Tundra Clips from 2024 Part 1.
76.9K7 -
1:05:19
Sarah Westall
9 hours agoDying to Be Thin: Ozempic & Obesity, Shedding Massive Weight Safely Using GLP-1 Receptors, Dr. Kazer
70.5K19 -
54:38
LFA TV
1 day agoThe Resistance Is Gone | Trumpet Daily 12.26.24 7PM EST
51.7K9 -
58:14
theDaily302
18 hours agoThe Daily 302- Tim Ballard
52.8K8 -
13:22
Stephen Gardner
11 hours ago🔥You'll NEVER Believe what Trump wants NOW!!
102K251 -
54:56
Digital Social Hour
1 day ago $10.83 earnedDOGE, Deep State, Drones & Charlie Kirk | Donald Trump Jr.
56.4K5 -
DVR
The Trish Regan Show
13 hours agoTrump‘s FCC Targets Disney CEO Bob Iger Over ABC News Alleged Misconduct
64.2K37 -
1:48:19
The Quartering
14 hours agoElon Calls White People Dumb, Vivek Calls American's Lazy & Why Modern Christmas Movies Suck!
143K112 -
2:08:42
The Dilley Show
14 hours ago $36.74 earnedH1B Visa Debate, Culture and More! w/Author Brenden Dilley 12/26/2024
123K42 -
4:55:59
LumpyPotatoX2
17 hours agoThirsty Thursday on BOX Day - #RumbleGaming
113K7