Premium Only Content
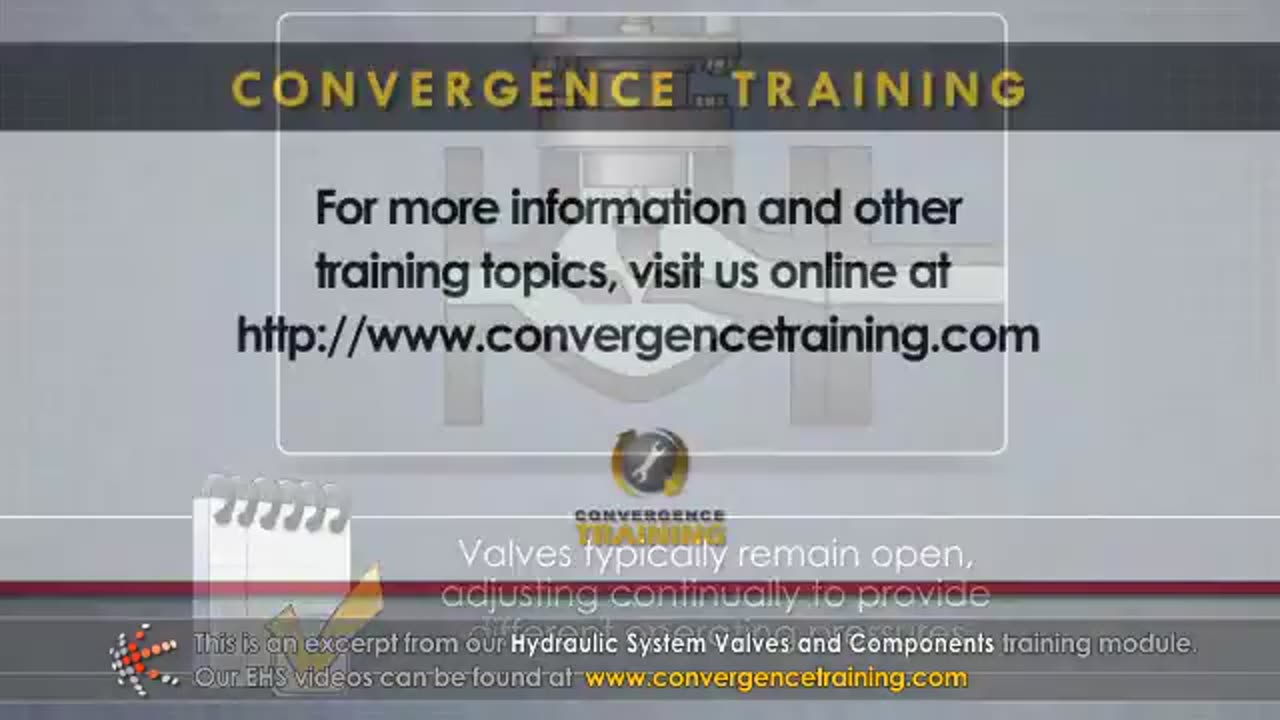
Hydraulic System Valves and Components
### **Hydraulic System Valves and Components: Key Elements in Fluid Control**
In hydraulic systems, **valves** and **components** play a crucial role in controlling the flow, pressure, and direction of the hydraulic fluid. These components ensure that hydraulic power is distributed effectively to perform tasks like lifting, pushing, rotating, or stabilizing in a controlled and safe manner. Here's an overview of the key **valves** and **components** used in hydraulic systems.
---
### **1. Hydraulic Valves: Functions and Types**
Hydraulic valves control the direction, pressure, and flow of hydraulic fluid within the system. They ensure that hydraulic energy is routed where it's needed and help maintain safety and efficiency.
#### **A. Directional Control Valves**
These valves direct the flow of hydraulic fluid to different parts of the system, determining the path the fluid takes.
- **Two-Way Valve:** Allows fluid to flow in one direction and return in another, typically used in simple systems (e.g., single-acting cylinders).
- **Four-Way Valve:** Directs fluid to different chambers in double-acting cylinders, controlling both extension and retraction.
- **Spool Valve:** A common type of directional valve, it uses a spool to block or direct the flow of fluid through different ports. It can be manually, electrically, or hydraulically controlled.
**Applications:**
- Operating cylinders and motors
- Dividing fluid flow to different actuators
- Changing the direction of motion in machinery
#### **B. Pressure Control Valves**
Pressure control valves are designed to regulate the system's pressure to prevent over-pressurization or to maintain the desired pressure range.
- **Relief Valves:** Protect the system by venting fluid back to the reservoir if the pressure exceeds a safe limit.
- **Sequence Valves:** Control the order in which pressure is applied to various parts of the system. They ensure that one actuator gets pressurized before another.
- **Unloading Valves:** Divert or "unload" fluid from a pump when it's not needed, reducing system load and conserving energy.
**Applications:**
- Preventing over-pressurization
- Ensuring proper pressure levels for efficient operation
- Managing multiple actuators in a controlled sequence
#### **C. Flow Control Valves**
Flow control valves regulate the flow rate of hydraulic fluid, controlling the speed of actuators.
- **Fixed Flow Control Valves:** These valves limit the flow to a constant rate regardless of pressure changes.
- **Variable Flow Control Valves:** These can adjust the flow rate depending on the operating conditions, providing greater flexibility.
**Applications:**
- Controlling the speed of linear or rotary actuators
- Adjusting the flow to specific components for optimal performance
#### **D. Check Valves**
Check valves allow flow in one direction while preventing reverse flow. This is critical for systems where fluid should only flow in one direction, such as in preventing backflow into a pump or actuator.
- **Types:** Ball check valves, poppet check valves, and non-return check valves.
**Applications:**
- Preventing backflow in hydraulic circuits
- Protecting sensitive components from reverse pressure
---
### **2. Hydraulic Actuators**
#### **A. Hydraulic Cylinders**
Hydraulic cylinders are the most common actuators in hydraulic systems. They convert the hydraulic energy (fluid pressure) into linear motion.
- **Single-Acting Cylinder:** Fluid is supplied to only one side of the piston. The cylinder moves in one direction, and a spring or gravity returns it to its initial position.
- **Double-Acting Cylinder:** Fluid is supplied to both sides of the piston, allowing movement in both directions. It is used for more precise control and higher force.
**Applications:**
- Lifting heavy loads (e.g., cranes, presses)
- Linear motion in automated machinery
#### **B. Hydraulic Motors**
Hydraulic motors convert hydraulic pressure and flow into rotational motion. They are used when the system requires rotary motion rather than linear motion.
- **Gear Motors:** Simple and cost-effective, gear motors provide low-to-medium torque output.
- **Vane Motors:** Provide smooth operation and medium-to-high torque output.
- **Piston Motors:** Used in high-torque, high-performance applications, these motors are highly efficient.
**Applications:**
- Rotary applications like conveyors, winches, or pumps
- Machinery requiring rotational force
---
### **3. Hydraulic Reservoir**
The **reservoir** stores hydraulic fluid and ensures there’s enough fluid available for the system. It also serves to cool and filter the fluid before it is sent back to the pump.
**Functions:**
- **Fluid Storage:** Provides a buffer to accommodate system fluid requirements and pressure changes.
- **Cooling:** Helps dissipate heat from the hydraulic fluid, which can become heated during operation.
- **Filtration:** Contains filters that remove contaminants from the fluid, preventing damage to sensitive components.
---
### **4. Hydraulic Accumulators**
A hydraulic **accumulator** stores energy in the form of compressed fluid or gas. It helps to smooth out pressure fluctuations, store energy, and provide backup power.
- **Bladder Accumulators:** Use a flexible bladder to separate the hydraulic fluid from a compressible gas (usually nitrogen).
- **Piston Accumulators:** A piston separates the fluid and gas and stores energy as hydraulic fluid is pressurized.
- **Diaphragm Accumulators:** Similar to bladder accumulators but use a diaphragm to separate the two fluids.
**Functions:**
- **Energy Storage:** Provide extra pressure or volume when the system demands it.
- **Pressure Stabilization:** Reduce pressure spikes and maintain stable system operation.
- **Emergency Backup:** Provide hydraulic power during system failure or pump downtime.
---
### **5. Hydraulic Filters**
Hydraulic filters keep the fluid clean by removing contaminants that can damage the pump, valves, or actuators. Filters are often placed in the suction line, return line, or pressure line.
- **Suction Filters:** Prevent contaminants from entering the pump.
- **Return Filters:** Clean the fluid as it returns to the reservoir.
- **Pressure Filters:** Protect sensitive components by filtering fluid under pressure.
**Functions:**
- **Contaminant Removal:** Protect the system from dirt, debris, and other particles.
- **Fluid Quality Maintenance:** Ensure the hydraulic fluid remains clean and effective for longer periods.
---
### **6. Hydraulic Pressure Gauges**
Pressure gauges are used to monitor the hydraulic pressure in the system. They provide valuable feedback for operators to ensure the system is operating within safe and optimal pressure limits.
**Functions:**
- **Pressure Monitoring:** Track real-time pressure levels for system health.
- **Safety Alerts:** Notify operators if pressure exceeds or falls below safe levels.
- **System Performance:** Help operators assess system performance and efficiency.
---
### **7. Hydraulic Hoses and Tubing**
Hydraulic hoses and tubes transport the hydraulic fluid between components. Hoses are flexible, while tubes are rigid. Both need to withstand high pressure and be resistant to wear, chemicals, and temperature fluctuations.
- **Hoses:** Flexible and made of reinforced rubber or synthetic materials, they are used where flexibility is needed.
- **Piping/Tubing:** Made of steel or aluminum, used in fixed installations where flexibility is not necessary.
**Functions:**
- **Fluid Transport:** Carry hydraulic fluid between pumps, actuators, valves, and other components.
- **Pressure Resistance:** Must withstand high-pressure fluid flow without failure.
---
### **8. Hydraulic Control Panels**
Hydraulic control panels are used to monitor and control the hydraulic system. These panels often feature gauges, switches, and buttons to operate pumps, valves, actuators, and other components.
**Functions:**
- **System Operation:** Operators can start, stop, or adjust the settings of hydraulic components.
- **Monitoring:** Display critical data like fluid pressure, temperature, and flow rate.
- **Safety and Alerts:** Provide feedback and warnings if the system is underperforming or at risk.
---
### **Conclusion**
Hydraulic systems depend on various **valves**, **actuators**, and **components** to function effectively. Each component, from directional control valves that manage fluid flow to actuators that convert hydraulic power into motion, plays a crucial role in ensuring the system operates safely and efficiently. Proper understanding and maintenance of these components can lead to improved system performance, extended equipment life, and safer operation in industrial, automotive, and construction settings.
-
1:25:53
Kim Iversen
3 days agoStriking Back: Taking on the ADL’s Anti-Free Speech Agenda
74K33 -
49:35
Donald Trump Jr.
12 hours agoA New Golden Age: Countdown to Inauguration Day | TRIGGERED Ep.202
154K170 -
1:14:34
Michael Franzese
10 hours agoWhat's Behind Biden's Shocking Death Row Pardons?
68.7K47 -
9:49
Tundra Tactical
9 hours ago $15.74 earnedThe Best Tundra Clips from 2024 Part 1.
88.6K7 -
1:05:19
Sarah Westall
9 hours agoDying to Be Thin: Ozempic & Obesity, Shedding Massive Weight Safely Using GLP-1 Receptors, Dr. Kazer
78.5K20 -
54:38
LFA TV
1 day agoThe Resistance Is Gone | Trumpet Daily 12.26.24 7PM EST
57.3K9 -
58:14
theDaily302
18 hours agoThe Daily 302- Tim Ballard
57.1K9 -
13:22
Stephen Gardner
12 hours ago🔥You'll NEVER Believe what Trump wants NOW!!
106K263 -
54:56
Digital Social Hour
1 day ago $10.83 earnedDOGE, Deep State, Drones & Charlie Kirk | Donald Trump Jr.
59.2K5 -
DVR
The Trish Regan Show
13 hours agoTrump‘s FCC Targets Disney CEO Bob Iger Over ABC News Alleged Misconduct
64.2K38