Premium Only Content
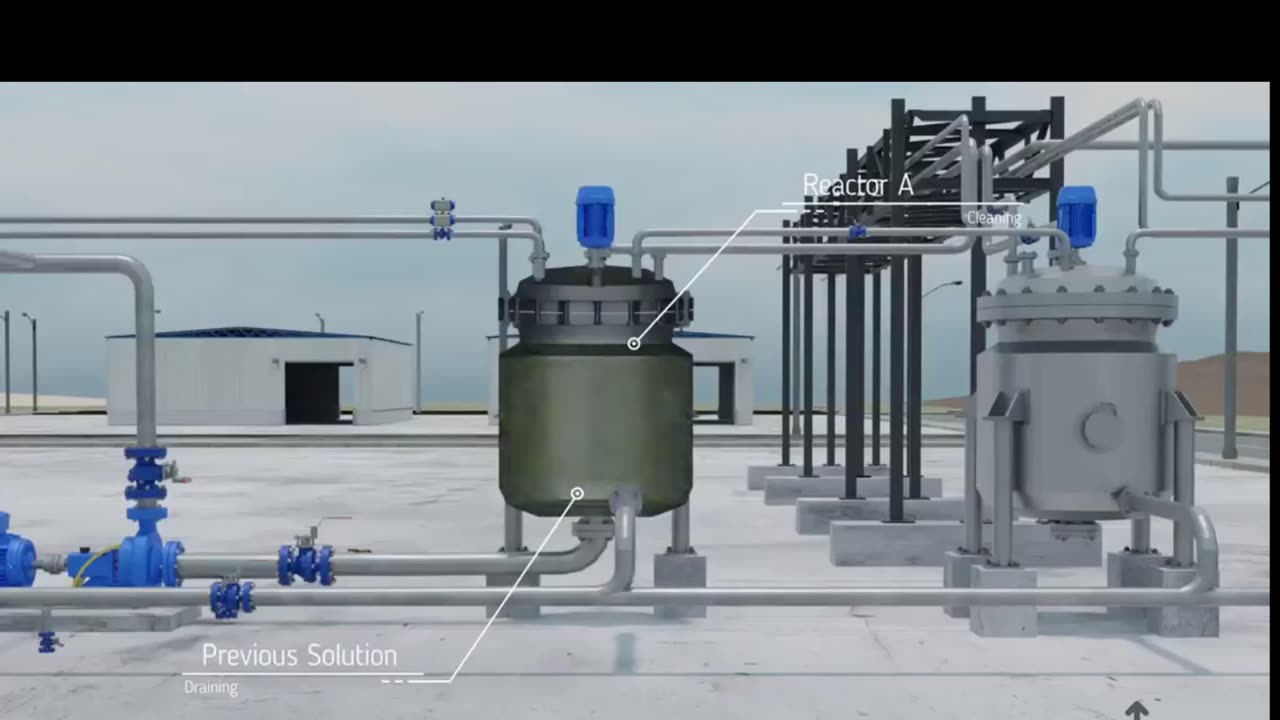
Mechanical Isolation of Process Piping & Equipment
Positive isolation ensures that process piping, equipment, or vessels are completely isolated from hazardous materials, making it impossible for these materials to enter the work area. This type of isolation eliminates the risk of accidental reconnection to the hazard source due to equipment failure or operator error.
Several methods can be used to achieve positive isolation, including:
A) Spool Removal or Air Gapping Isolation:
This method involves line-breaking by removing a section (spool) from the piping and installing a blind flange to block any flow from the source.
B) Blind Isolation:
Blind isolation refers to the insertion of a blind (spade) between two flanges. When spool removal is challenging, valve and line-rated spade isolation offer a high level of safety.
All isolations should remain secure for the duration of the maintenance or activity and be tested to confirm their effectiveness.
C) Double Block & Bleed Isolation:
Considered the most secure valve isolation method, the Double Block and Bleed (DBB) system features two valves in series with a bleed valve in between, allowing any pressure or material between the two valves to be bled safely through a vent.
General Rules for Isolations:
Always use the valves closest to the equipment.
Some equipment is dangerous if valves used for isolation are not operated in the correct sequence.
Do not block Pressure Safety Valves until the equipment is fully depressurized, and ensure adequate venting to prevent over-pressurization.
Avoid trapping gases or liquids in sections without pressure protection or thermal release, as pressure build-up from temperature increases can cause catastrophic equipment failure.
🚫 Note: Avoid using single block valves to isolate hazardous energy sources, as valves can leak, even if newly installed.
-
7:44
Tactical Advisor
16 hours agoBest Budget Benelli Shotgun | Orthos v Panzer Arms
1.06K -
6:09
BIG NEM
8 hours agoThe Dark Truth About My Balkan Uncle's Past
6481 -
52:06
Uncommon Sense In Current Times
18 hours ago"Gerrymandering Markets: A Deep Dive with Robert Bork Jr. into Biden's Antitrust Agenda"
853 -
1:02:49
The Tom Renz Show
11 hours agoThe Democrats LA Fires & COVID Grand Jury
1.68K -
47:49
PMG
15 hours ago $0.02 earned"There Ain’t No Grace in It! What to do when you’re worn out!"
1.49K1 -
3:19:06
FreshandFit
6 hours agoAnnoying HOES Kicked Off After HEATED Debate On Rape Culture!
62.1K52 -
57:00
PMG
15 hours ago $10.86 earned"Terror Attacks or False Flags? IT DOESN'T ADD UP!!!"
37.4K12 -
1:14:42
Anthony Rogers
12 hours agoThoughts on the L.A. Fires
55K16 -
2:37:32
Kim Iversen
11 hours agoTerrorism, Act of God or “Newscum” Incompetence: What REALLY Fueled The California Wildfires
69.3K216 -
2:16:33
Tucker Carlson
9 hours agoTucker Carlson and Michael Shellenberger Break Down the California Fires
230K352