Premium Only Content
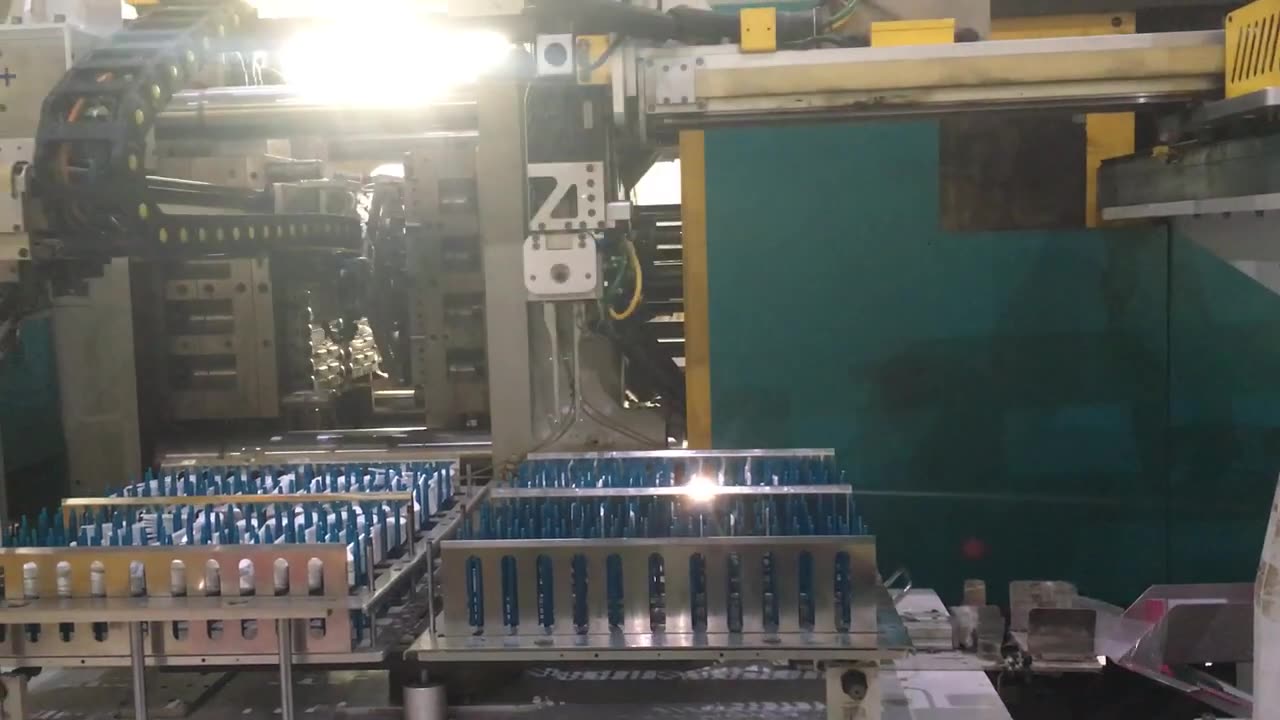
Plastic cutlery Injection Machine
Plastic cutlery Injection Machine
Plastic cutlery injection molding machines are used in the manufacturing process of producing plastic utensils such as forks, knives, and spoons. These machines operate through the injection molding process, which involves melting plastic pellets and injecting the molten material into a mold cavity to form the desired shape. Here is an overview of the key components and steps involved in the plastic cutlery injection molding process:
Key Components of a Plastic Cutlery Injection Molding Machine:
Injection Unit:
This unit is responsible for melting and injecting the plastic material into the mold.
It includes a hopper for holding plastic pellets, a barrel for heating and melting the plastic, and a screw or plunger for injecting the molten plastic into the mold.
Mold:
The mold is a crucial part of the process, as it defines the shape and features of the plastic cutlery.
It consists of two halves (cavities) that come together to form the final product.
Clamping Unit:
The clamping unit holds the mold in place during injection and cooling.
It includes a clamping mechanism to securely close and hold the mold halves together.
Cooling System:
After injection, the plastic inside the mold needs to cool and solidify.
A cooling system helps regulate the temperature and speed up the solidification process.
Ejector System:
Once the plastic has solidified, the ejector system pushes the finished plastic cutlery out of the mold.
Control System:
The control system manages and regulates the entire injection molding process, including temperature control, injection speed, and other parameters.
Plastic Cutlery Injection Molding Process:
Material Loading:
Plastic pellets are loaded into the hopper of the injection molding machine.
Injection:
The plastic pellets are melted in the barrel and injected into the mold cavity.
Cooling:
The molten plastic inside the mold cools and solidifies to take the shape of the cutlery.
Ejection:
The ejector system pushes the finished plastic cutlery out of the mold.
Quality Control:
The produced plastic cutlery undergoes inspection for defects, ensuring quality standards are met.
Packaging:
The final step involves packaging the plastic cutlery for distribution.
When seeking a plastic cutlery injection molding machine, it's essential to consider factors such as the machine's capacity, precision, energy efficiency, and the type of plastic materials it can process. Manufacturers and suppliers of plastic molding machines can provide specific details about their equipment, and you may also explore industry exhibitions and trade shows to learn more about available technologies.
-
17:30
Bearing
8 hours agoTHIS is why Men Shouldn’t Compete in Women's Sports 🤣
6.4K47 -
13:19
VSOGunChannel
1 day ago $1.18 earnedI've Never Cleaned This Gun
10.6K2 -
16:19
DeVory Darkins
21 hours ago $10.15 earnedWoke activist dealt HUGE BLOW after judge approves deportation
20.9K94 -
9:55
Russell Brand
1 day agoThis Is Absolutely Shocking...
66.6K79 -
26:01
The Brett Cooper Show
2 days ago $3.48 earnedChappell Roan Says All Parents Are Miserable. Is She Right? | Episode 21
19.5K26 -
1:34:25
Michael Franzese
19 hours agoThey Blame Trump for Everything - But Who’s Really Wrecking the Economy?
56.1K61 -
1:43:55
I_Came_With_Fire_Podcast
14 hours agoThe REVOLUTION to SAVE AMERICA Starts At HOME
45.3K9 -
28:33
Mike Rowe
3 days agoWhy Are Healthy Men Exiting The Workforce? | Nick Eberstadt #274 | The Way I Heard It
49.3K211 -
38:40
Adam Carolla
2 days ago $12.77 earnedBill Maher Calls Trump 'Effective'?! You won't see it coming! | Adam Carolla Show | #news
77.2K32 -
14:40
Talk Nerdy Sports - The Ultimate Sports Betting Podcast
5 hours ago4/12/25 - Wake the F Up: It’s Saturday! It’s War!
35.5K4