Premium Only Content
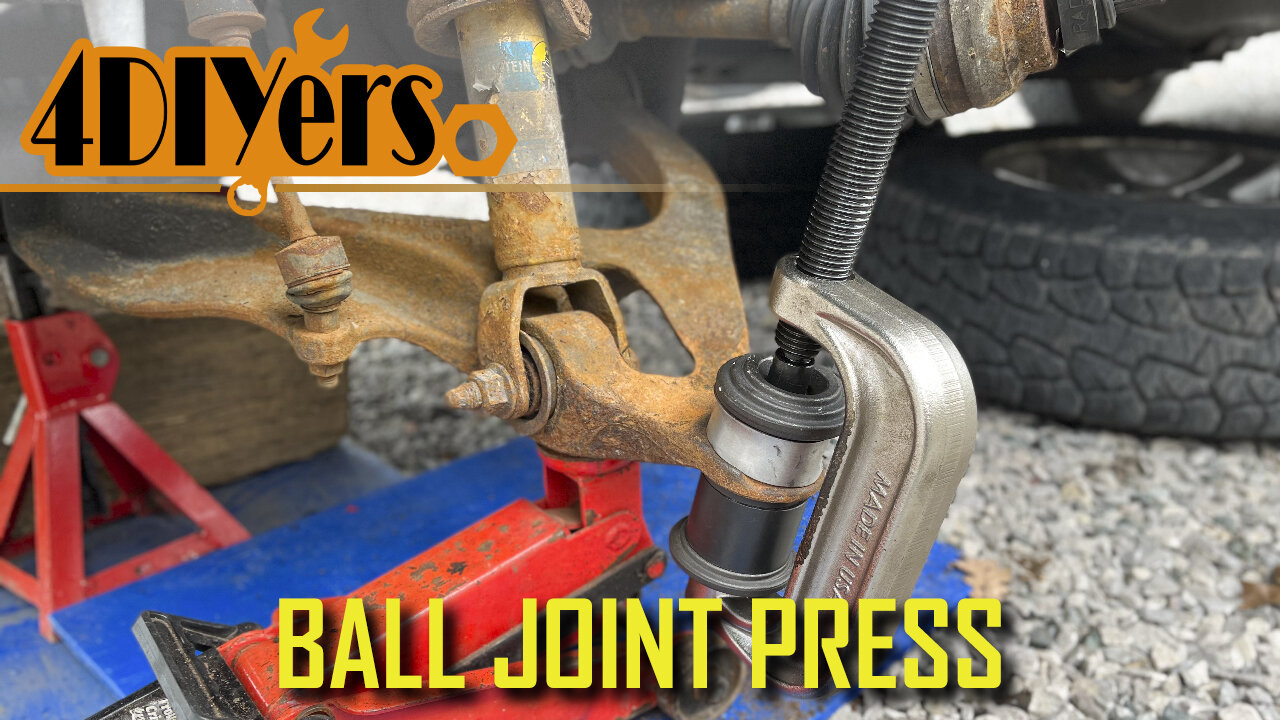
How to Use a Ball Joint Press
How to use a ball joint press. This video includes the removal and installation of the pressed in ball joints into a control arm. For this example I will be using my 2006 dodge ram. Here I’m using my OTC kit model number 7249, there are various kits available. It’s always important to invest in something which is a good quality so it doesn’t let you down part way through a job #balljoint #suspension #mechanic
Amazon OTC ball joint press links
USA: https://amzn.to/3zAGimp
Canada: https://amzn.to/3JbsZvO
Website: http://4diyers.com
Patreon: https://www.patreon.com/4diyers
Facebook: https://www.facebook.com/4diyers
Twitter: https://twitter.com/4DIYers
Instagram: https://www.instagram.com/4diyers/
Tumblr: http://4diyers.tumblr.com
Pintrest: https://www.pinterest.com/4diyers/
Tools/Supplies Needed:
-ball joint press
-ball joint separator
-hammer
-gear oil
-new ball joints
-pliers
-ratchet and socket set
Procedure:
Remove the wheel, procedures for accessing the ball joint will vary between vehicles. Considering this truck is four-wheel drive, I will be removing the steering knuckle to access the lower ball joint. Therefore the axle needs to be disconnected.
Ball joints may be equipped with a stover nut or castle nut. In the case of a castle nut, a cotter pin will need to be removed. The cotter pin needs to be straightened out and then pulled through the whole using pliers.
To disconnect the taper on the ball joint from the steering knuckle, a ball joint separator is used. You can also hit the start with the hammer or use a pickle fork. This is an aluminum steering knuckle, do not hit it with a hammer as you do risk cracking it.
Use the ball joint separator to disconnect the lower ball joint. When removing the steering knuckle, the spline will need to be disconnected from the wheel bearing on this four-wheel-drive truck.
Using a wire brush, clean around the ball joint. This will remove any debris so we can determine if a clip is required to be removed and no debris binds up around the ball joint when it’s being pressed out of its position.
Using snap ring pliers, remove the snap ring. Ross can sometimes hold these snap rings in place so the assistance of a standard screwdriver may be required.
This is a serviceable ball joint, the grease fitting will need to be removed. With this removed, we will have a flat surface for the press to push on.
Oil the threads on the press using gear oil. This will ensure there is no binding and you’re not causing any damage to the threads of the press.
The ball joint will have a lip on the one side where it holds it into place. On the opposite side is where the snap ring is located. The snapper inside is where the ball joint is pushed from. The threaded rod will push down onto the ball joint, on the other side there will be a sleeve and a face plate where the opposite side of the C frame of the press locks on to. When the press is tightened, this will push the ball joint down and it has free space for movement within that sleeve. The sleeve should be larger than the ball joint retaining ring.
Once that ball joint has been removed, use a wire brush to clean up any rust or debris around the face and inner bore of where that ball joint would be located.
Always ensure the attachments for your ball joint press is clean. This particular ball joint doesn’t have a boot installed at the moment, this will be installed after. There is exposed grease and contaminants can stick to this.
Use a sleeve that can fit on the ring of the ball joint. You’ll need free space so the ball joint can push through without any obstructions.
Depending on the distance, you may need to change attachments as the press doesn’t open up wide enough. Tighten the press so the ball joint is slowly pushing in. Remove the ball joint press so you can switch attachments to fully push through. Tighten the ball joint press until that ball joint is fully seated.
Install the boot to protect the joint. This particular brand does come with an installation cup to push on the boot.
If you have a serviceable ball joint, the next step is installing the grease fitting. Make sure the grease fitting is angled in such a way so it doesn’t interfere with the steering knuckle and can be easily accessed.
Using snap ring pliers, install the new snap ring for the ball joint. A standard screwdriver may be required to help push down that snap ring and shirts for seated.
Install all other parts in reverse of removal.
Thank you to all those who watch my videos and support my content. Don't forget to subscribe to my channel for future tutorial videos and like my video if you found it helpful. New videos are always being uploaded every week!
© 4DIYers 2013
All Rights Reserved
No part of this video or any of its contents may be reproduced, copied, modified or adapted, without the prior written consent of the author.
-
57:42
Flyover Conservatives
1 day agoThe Great Gold Cover-Up: Is Fort Knox EMPTY?! - Clay Clark + Dr. Kirk Elliott | FOC Show
63.2K19 -
1:24:40
Kim Iversen
15 hours agoJeffrey Sachs Just Exposed the Truth They Don’t Want You to Hear
80.1K106 -
2:11:32
Glenn Greenwald
13 hours agoGlenn From Moscow: Russia Reacts to Trump; Michael Tracey Debates Ukraine War | SYSTEM UPDATE #413
186K107 -
2:19:23
Slightly Offensive
13 hours ago $15.38 earnedGOV. RAMASWAMY? Vivek to import 1 BILLION INDIANS to OHIO | Nightly Offensive
97.1K55 -
4:51:08
Wahzdee
16 hours agoSniper Elite Then Extraction Games—No Rage Challenge! 🎮🔥 - Tuesday Solos
110K3 -
2:12:58
Robert Gouveia
15 hours agoSenator's Wife EXPOSED! Special Counsel ATTACKS; AP News BLOWN OUT
117K80 -
55:07
LFA TV
1 day agoDefending the Indefensible | TRUMPET DAILY 2.25.25 7PM
65.9K21 -
6:09:26
Barry Cunningham
22 hours agoTRUMP DAILY BRIEFING - WATCH WHITE HOUSE PRESS CONFERENCE LIVE! EXECUTIVE ORDERS AND MORE!
202K77 -
1:46:37
Game On!
17 hours ago $7.46 earnedPUMP THE BRAKES! Checking Today's Sports Betting Lines!
109K4 -
1:27:21
Redacted News
16 hours agoBREAKING! SOMETHING BIG IS HAPPENING AT THE CIA AND FBI RIGHT NOW, AS KASH PATEL CLEANS HOUSE
251K329