Premium Only Content
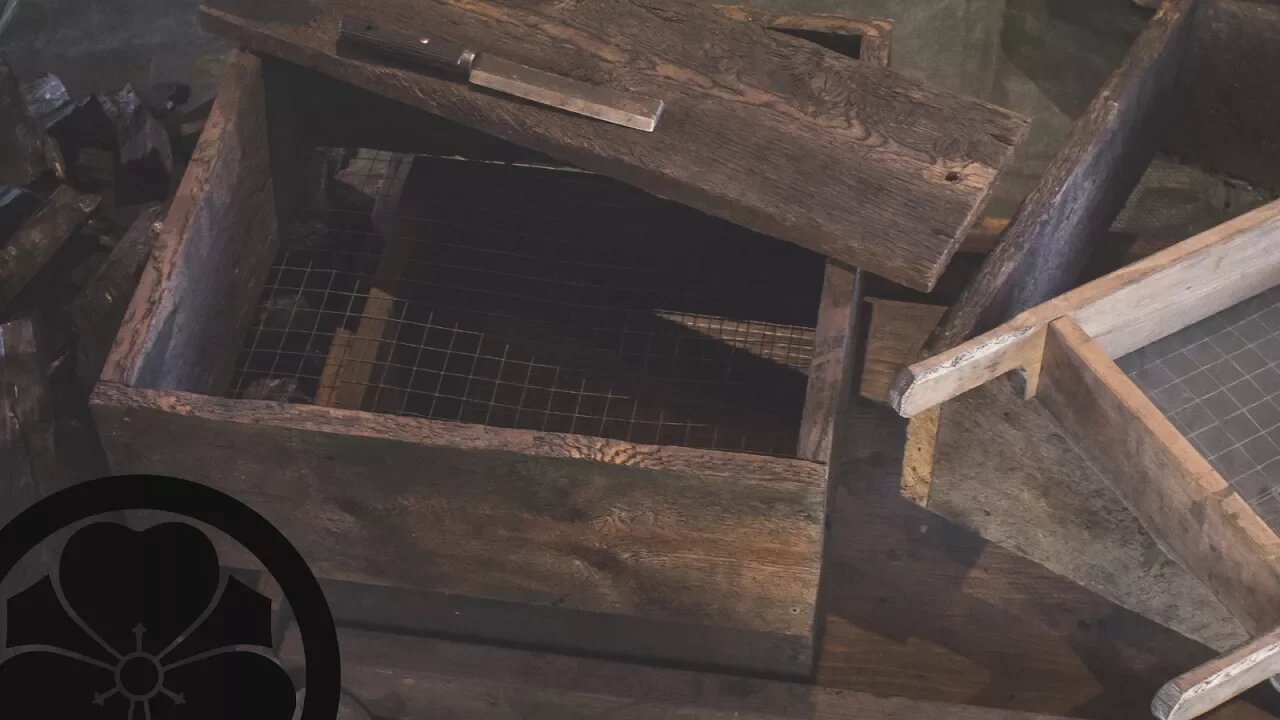
Sumi-kiri - chopping charcoal for bladesmithing
Read more about the museum project here: http://islandblacksmith.ca/2017/01/building-traditional-swordsmith-forge/
See more charcoal making videos here: https://www.youtube.com/playlist?list=PLBJ5AOs7cMwAi0VcrZt-tyGIsrOUrzhyj
A sample of the sumi-kiri process; charcoal chopping, screening, and sorting techniques, and may offer some useful details for astute observers.**
Traditional Japanese swordsmithing forges are fueled by softwood charcoal which is first chopped, screened, and sorted into several sizes for different stages of the forging process.
The charcoal is chopped and then processed through four sizes of screen, the largest is for tanren, the second for hizukuri (I tend to use the largest for hizukuri as well and keep the second size mainly for yaki-ire), the third size isn't highly useful but may be crushed into fines or saved for tatara, the fourth is the fines for lining the bottom of the forge, and the remainder is dust for mixing into yaki-ire clay or for brasque refractory.
Measurements for the screen sizes are given in sun-shaku and the type of charcoal they keep in is listed rather than what they allow to pass through.
3.03022 cm
= 0.1 shaku(尺)
= 1 sun(寸)
= 10 bu(分)
= 100 rin(厘)
**Three things to note, 1. after setting up, i moved the camera orientation 180 degrees and rather than move all of the charcoal i moved only the chair to the opposite side, but for efficiency it is a good idea to have the charcoal at the left side within reach of the non-chopping hand...2. rather than chopping directly into a screen as i do, the normal procedure is to chop onto the tarp and then rake most of the largest charcoal off the top by hand before screening the remaining pile (https://youtu.be/3DdXdxSb3vE)...3. also, some of this charcoal is quite soft having been heated too quickly in the kiln or overcooked so it looks more crumbly than it should.
-
1:03:11
Miss Understood With Rachel Uchitel
4 days agoDefending the Indefensible: The Man Behind the Most Controversial Cases – Attorney Norm Pattis
421 -
LIVE
The Pete Santilli Show
14 hours agoDEM CONGRESSMAN’s STAFFER IMPERSONATED FBI & STEPS FROM TRUMP WITH GUN ON JAN 6 [EP 4436-8AM]
1,759 watching -
LIVE
Game On!
12 hours ago $0.79 earnedTop 5 reasons NFL experts believe the Eagles will win Super Bowl 60!
1,519 watching -
14:45
EvenOut
16 hours ago $2.45 earnedEndless Checkout At a Grocery Store!
24.4K4 -
4:36
Misha Petrov
14 hours ago“Bikinis and Burgers” Return! Carl’s Jr. Super Bowl Ad – A Win or Just More Hypersexualization?
28.8K28 -
9:10
MichaelBisping
23 hours agoBISPING: 'SHUT UP ABOUT CANELO!' | Jake Paul vs Canelo Alvarez?!
17.4K2 -
37:17
inspirePlay
22 hours ago $1.15 earned🏆 The Super Bowl is Over… But Who REALLY Called It? 🏌️♂️🔥
11.8K4 -
19:42
Degenerate Jay
22 hours ago $0.29 earnedThe Flash Video Game Cancelled... Again
10.1K1 -
7:25
State of the Second Podcast
22 hours agoWho Won’t Make it Through the Trump Slump?
25.6K5 -
52:36
Bek Lover Podcast
15 hours agoKanye West Meltdown & More Strange News w/ @THEREALBRADLEA & @TheBekLoverPodcast
30.3K15