Premium Only Content
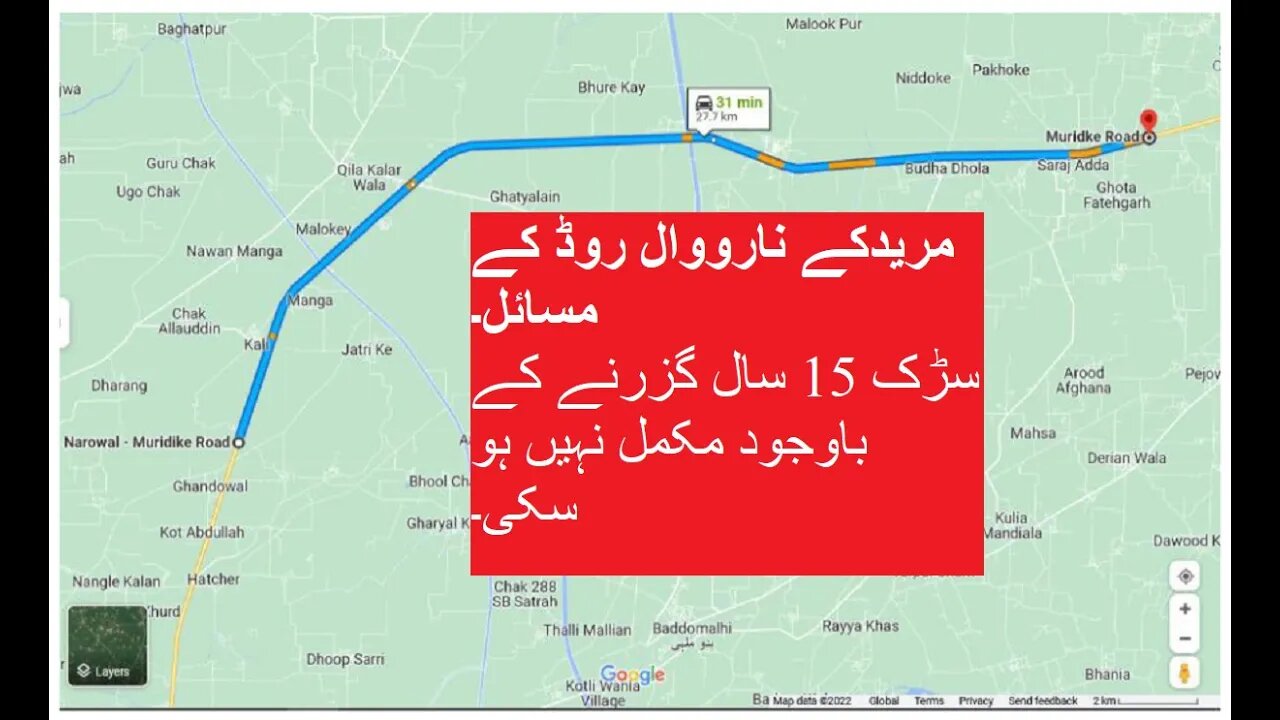
Defects in Muridke Narowal Road Project مریدکے نارووال روڈ کے مسائل۔
Defects in Muridke Narowal Road Project
مریدکے نارووال روڈ کے مسائل۔ سڑک 15 سال گزرنے کے باوجود مکمل نہیں ہو سکی۔
The scheme was behind schedule as the physical progress of work was observed to be
lesser than the planned progress (Table 8, Figure 5).
• Planned Physical Progress: 95% as of Sep, 2022
• Actual Physical Progress: 60%
• Actual Financial Progress: 65%
At such a pace of work, the project may be delayed while the project cost may be
enhanced due to differences in the physical and financial progress and variance at
completion as illustrated in Table 7 under Earned Value Analysis.
8.2 Cost:
2. The financial utilization of FY 2022-23 is 0% due to the no progress of work at site
and blacklisting of the contractor, as shown in Table 5.
3. The funds could not be allocated as of financial phasing of PC-I document and only
70% of the project funds are allocated on completion of 95% planned duration of the
project, as shown in Table 5.
8.3 Risks and Constraints:
4. The slow progress of work may result in delayed completion of the project and price
escalation.
8.4 Scope
5. The errors in measuring the length of the road during field survey needed to be
rectified as it is observed through satellite measurement that the length of the road is
27.7km (Annex-A) instead of 33.21km as measured by surveying team.
6. The project informatory board required to be fixed at site of work.
7. The key project stakeholders are required to be present at site of work to present the
field and progress data.
8. The side slope required to be stabilized and water standing in Right of Way needed
to be removed, as shown in Figure 6.
9. The loose material needed to be compacted on the approaches of the road while toe
width is required to be as per required drawings, as shown in Figure 7.
10. The workmanship needed to be improved and defects in concreting is needed to be
rectified, as shown in Figure 8.
14 | P a g e
11. The wing wall is required to be constructed near the bridge abutments and finishing
and clearing works are required, as shown in Figure 9.
12. The wing wall is required and batten boards are needed to be provided in the joints
of RCC, as shown in Figure 10.
13. The level of water drainage pipe needed to be raised to drain the water after asphalt
laying, as shown in Figure 11.
14. The construction joints are required to be fixed during the concreting, as shown in
Figure 12.
15. The clearing works are required on the deck slab of the bridge, as shown in Figure
13.
16. The under-construction bridge required to be cordon off with proper barriers to avoid
any unforeseen incident, as shown in Figure 14.
17. The electric pole needed to be shifted away from main carriage way, as shown in
Figure 15.
18. The road furniture, cat eyes, road marking and sign boards required, as shown in
Figure 16.
19. The safety barrier required to be provided to avoid accidents, as shown in Figure 17.
This road causing causalities due to non-adoption of standard safety practices and
data of causalities and road incidents are enclosed in Annex-B.
20. The clearing and grabbing works required, as shown in Figure 18.
21. The encroachments are needed to be removed, as shown in Figure 19.
22. The damaged parts are needed to be rectified on priority bases, as shown in Figure
20.
23. The wing walls are required to be provided in the culvert to avoid scouring due to
rain water, as shown in Figure 21.
8.5 Health, Safety & Environment
24. The workers are required to be provided with Personal Protecting Equipment (PPEs).
25. The safety equipment such as safety ribbons, and safety signs are required to be fixed
at the site and safety lights should be fixed at site for precautionary measures at night
time. Housekeeping needed to be done, while proper mobilization required to be
done at the site of work with the provision of safe drinking water to the human
resources.
8.6 Quality Control
26. The quality control plans, quality checklists and methodologies are required to be
documented at the site of work.
15 | P a g e
27. The standard laboratory should be furnished at site of work to control the quality of
work.
28. The technical staff of both contractor, consultant and client need to be present at site
of work.
29. The documents related to quality control testing as narrated below are required to be
maintained at the site of w
-
14:34
Misha Petrov
13 hours agoTikTok’s WOKE “Mean Girl” Is Insufferable
11.5K9 -
10:46
Mike Rowe
22 hours agoRiley Gaines Was Right All Along | The Way I Heard It with Mike Rowe
29K26 -
25:19
SB Mowing
1 day agoI had to do a DOUBLE TAKE because I couldn’t see the house at first
16.7K4 -
2:37:42
FreshandFit
12 hours agoGreg Doucette Guessed Their Body Fat Percentages And THIS Happened...
102K85 -
5:08:30
Akademiks
12 hours agoKendrick Lamar SPEAKS for first time SINCE BEEF in new Interview. Drake preppin new album. YE WYLING
146K24 -
2:12:17
Tucker Carlson
13 hours agoMike Benz Takes Us Down the USAID Rabbit Hole (It’s Worse Than You Think)
256K633 -
1:47:17
Roseanne Barr
17 hours ago $34.83 earnedThe Most Offensive Comic, Leonarda Jonie | The Roseanne Barr Podcast #86
149K167 -
4:17:42
Joker Effect
13 hours agoRumble Community Night. Reviewing Rumble partnership program, it's streamers and community discussion.
93.1K14 -
2:29:56
Laura Loomer
14 hours agoEP100: MAGA Goes Scorched Earth On USAID
88.1K53 -
51:45
Talk Nerdy 2 Us
15 hours ago🔥 Talk Nerdy 2 Us – Feb 7th: HACKED, TRACKED & UNDER ATTACK! 🔥
114K8