Premium Only Content
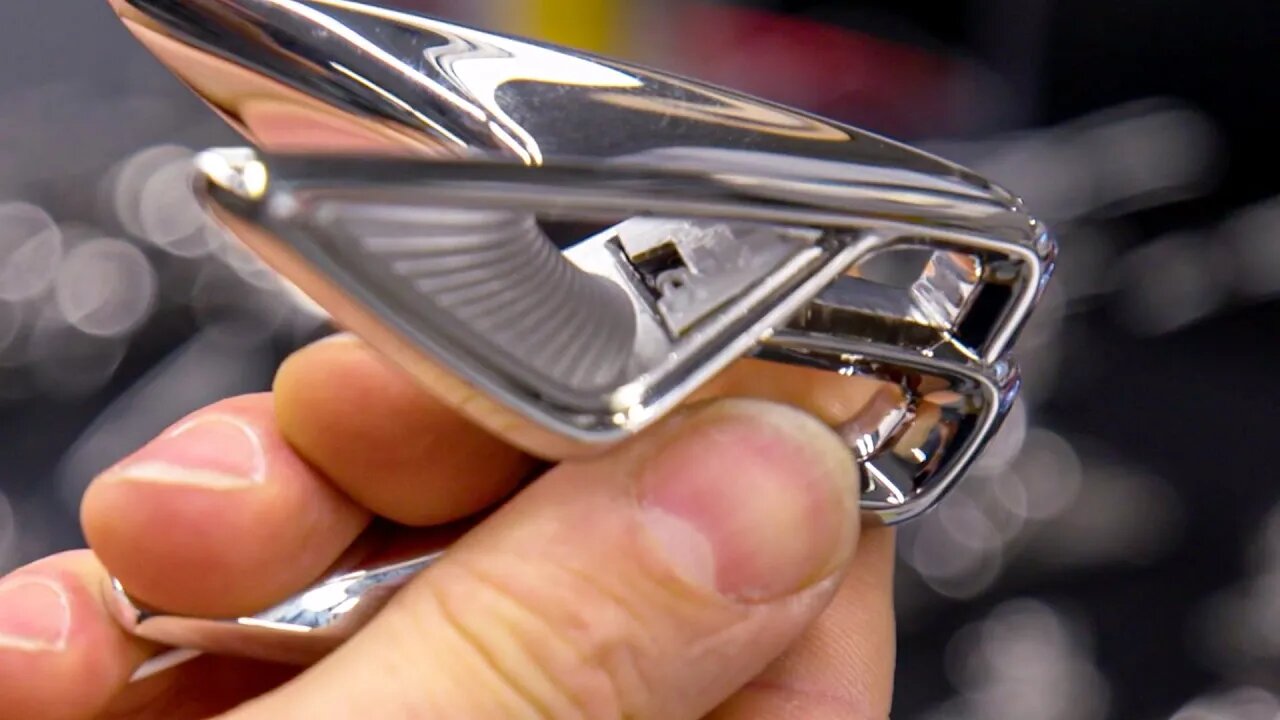
Bentley ‘Flying B’ Hood Ornament PRODUCTION
The Bentley ‘Flying B’ bonnet mascot is cast as a single piece of 316 grade stainless steel, which has an austenitic crystalline structure that’s both very tough and capable of withstanding extremes of temperature. The addition of molybdenum also gives it corrosion resistance, vitally important for a component that’s exposed to the elements all year round anywhere from the arctic circle to the equator.
The ‘Flying B’ is made using the investment (lost wax) casting process at Lestercast Ltd, a technique usually reserved for precision components such as gas turbine blades. This form of casting, though time consuming, is typically used for making complex-shaped components that require tighter tolerances, thinner walls and a better surface finish than can be obtained with sand casting.
First, molten wax is injected into a die. A water-soluble core occupies the cavity where the two acrylic crystal wings will sit, while a ceramic central core creates a passage within the wax moulding for the illumination wiring. The wax emblem is then removed from the die and the soluble core dissolved to create a perfect ‘Flying B’ in wax.
Next, the wax emblem is encased in multiple layers of a fine ceramic solution containing colloidal silica and alumina; once these layers have set solid, the wax is melted in a steam pressure chamber to leave a ceramic mould with a hollow cavity in the shape of the emblem.
At this point molten 316 stainless steel, heated to 1,600°C, is poured into the ceramic mould. Once the steel has cooled and set, the ceramic outer skin is removed, while the ceramic core is dissolved under pressure using a caustic solution. The stainless-steel Flying ‘B’ emblem that emerges is then ready for the next stage; shot blasting removes any minute traces of ceramic material and a process called ‘extrude honing’ ensures that the internal passage within is smooth enough for the wiring that will pass through it.
Only after every trace of ceramic material is removed, and the component carefully measured to ensure it meets the precise tolerances required, will the Flying ‘B’ be sent for hand polishing. This final touch of hand craftsmanship brings out the deep lustre of smooth stainless steel.
The entire process takes 11 weeks from start to finish, at which point the mascot is ready for assembly by WCM Europe Ltd, of the crystal acrylic wings, wiring and tiny LEDs that create such a magical effect when deployed.
Do you like it?
Comment, like, dislike, share!
Subscribe now: https://goo.gl/5i54Vg
✅ Source: Bentley
🎵 MUSIC used
Epidemic Sound ► https://bit.ly/2OvT1SC (30 days free)
Artlist ► https://artlist.io/JEAN-PAUL-784473 (60 days free)
-
1:15
CAR TV
11 months ago $0.10 earnedBMW 5 Series (2023) Crash Test
7.49K2 -
1:04
Do a Good Turn
2 years agoBirdhouse Ornament
12 -
0:17
liushu123
2 years agoModern production
8 -
0:11
adsafghhj
2 years agoAutomatic production workshop
2 -
0:29
Hdsfcdsc
2 years agoFood production video
11 -
5:14
DigivilleChannel
2 years agoVideo Production For Dummies
4 -
1:26
HometakesFL
2 years ago1226 NW Bentley Cir
2 -
1:14:19
The Anthony Rogers Show
16 hours agoEpisode 248 - Light Language & Intergalactic Gifts In The Higher Realms
83.7K8 -
2:38:12
Tundra Gaming Live
11 hours ago $5.86 earnedThe Worlds Okayest War Thunder Stream
55.4K1 -
10:57
Tactical Advisor
15 hours agoNEW Compact Echelon | Springfield 4.0 C (FIRST LOOK)
84.6K1