Premium Only Content
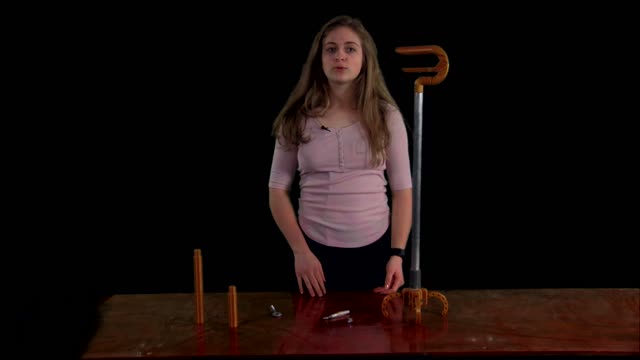
SuperCane
SuperCane
Copley High School
February 23rd, 2019
The Super Cane is a reimagined and redesigned multipurpose walking cane which combines three simple assistive devices into one easy to use tool. The devices that have been combined include: a free standing walking cane, grabber, and magnetic pickup tool. This device enables the user to only carry one device instead of three. The Super Cane is convenient, easy to use and durable.
The Copley High School (CHS) Engineering Team developed the Super Cane after a friend’s grandparent fell when she was picking up a piece of clothing off the ground. The grandparent needed to use a walking cane all the time as a result of her limited mobility. The team set out to design, develop and fabricate a device that she could not only use to walk but also to pick up everyday objects such as clothes, bottles, coffee mugs and even small metal objects such as keys or even silverware. What the team designed was a fully 3D printable, highly durable Super Cane.
The Super Cane is a hybrid, and when it comes to its construction, it can be completely 3D printed. However, in order to make it durable and effective, the fasteners, spring, center shaft, and flex point were all made from off the shelf, easily accessible materials which were sourced at Home Depot. Many prototypes were designed, fabricated and tested (virtually, through CAD software and physically) with varying results. The team determined, through this testing, that the best Super Cane Design had four claws, for freestanding stability, with embedded magnets and an aluminum shaft. The team also designed and tested three jaw designs with and without a segmented 3D printed shaft. Both designs incorporate a simple, strong, lightweight, ergonomic design as well as sharing all the same off the shelf parts.
The final part designs meet the competition design requirements, capability of our printers (size and tolerance), and material strengths. First, the CHS engineering team used SolidWorks to develop and virtually test the function and strength of the device using 3D CAD Models. Second, the device was to big to be printed by GrabCAD, so the team took the big parts and broke them down into smaller parts (to meet the GrabCAD requirements). For example, the handle is larger than the design specifications allow, as well as difficult to print without support with its curved surfaces, so to remedy this, the team cut the handle in half, sectioned it, tabbed it and indexed it. These changes worked as planned, so all the team had to do was glue all the parts together after they were printed. The final piece the team had to consider when designing and printing the parts was the Tolerance of the 3D printer. The team wanted all the parts to easily fit together and be glued as well as to thread the fasteners into the individual parts. The threading was simple; a screw and thread chart was used to calculate the hole size for a ¼ - 20 screw, and then the team tapped out the hole. Getting the parts to easily fit together was more difficult, but the team eventually designed and made all the mating parts .01” smaller / larger and chamfered all mating corners. This adjustment made it close to accurate, but some fitting was still necessary as with any prototype. All the prototypes resulted in a Super Cane that was designed, developed, tested and shared to help the grandparent as well as many other people who may need an assistive device.
3D Printing Method
To print the prototypes, the team converted the .stl files to G-Code using Matter Control. The .stl files were imported into the software and orientated on the printer table so that they would lay flat and not require any type of support material. At this point the parts were ready to be converted to G-Code, exported to a flash drive and taken to the printer to be printed. The 3D printer that the team used to print the prototype was a Rostock MAX V3 delta style printer with Atomic True Gold v2 - PLA filament. After the team went through a series of testing, they concluded that the printer settings that offered the best balance for strength, print speed and quality are as follows.
Atomic True Gold v2 - PLA (1.7653 avg. dia.)
Nozzle Diameter - 0.5mm
Bed Temp - 50 Degrees
Extruder Temp. - 210 Deg.
Retraction - 4mm
Extrusion Multiplier - 1.01
Layer Height - 0.02mm
Top / Bottom Solid Layers - 1mm
Fill Density - 30%
Infill Type - Triangles
Raft / Support - None
-
59:38
BEK TV
11 hours agoMedical Mysteries Revealed. What Mel Gibson and Joe Rogan were Afraid to Say
2.41K -
LIVE
LFA TV
12 hours agoALL DAY LIVE STREAM - WEDNESDAY 4/30/25
5,660 watching -
1:43:51
Chicks On The Right
4 hours agoTrump's contentious ABC interview, Trump's truths and trolls, and is AOC gonna run for president?
8.99K6 -
25:15
Producer Michael
17 hours agoTOURING A $10,800,000 LAS VEGAS MODERN MANSION!
32.8K9 -
1:57:01
BEK TV
1 day agoTrent Loos in the Morning 4/30/2025
32.1K1 -
15:35
The Illusion of Consensus
1 day agoRav Arora Warns Danger of Mass Immigration In Canada
24.2K11 -
26:33
CatfishedOnline
1 day agoI Sent $150k And Sold My Home For Online Love!
62.3K17 -
7:37
The Shannon Joy Show
14 hours ago💀 Doctor Death: NY’s Suicide Bill
38.2K14 -
19:05
This Bahamian Gyal
17 hours agoWhy would SHANNON SHARPE risk EVERYTHING for THIS?
38.3K6 -
34:53
Uncommon Sense In Current Times
18 hours ago $3.90 earnedEconomist Breaks Down Trump Tariffs | Dr. Jonathan Newman
44.8K19